Liquid Chrome Vs. Chromic Acid Flake
Contemplating how to continue offering chromic acid services in an increasingly stringent regulatory world? Liquid chrome products may be the solution you’re looking for.
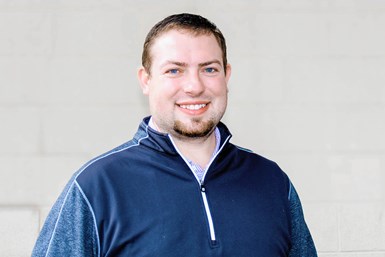
Richard Held is a surface finishing sales manager for Haviland Enterprises Inc. Visit havilandusa.com.
Q: Decorative and functional hexavalent chrome is a process that has been increasingly difficult to run but is still required for some applications within the industry. What are some ways that we can continue to provide this service, but limit the impact to our business with the increased safety and regulatory requirements?
In the face of increasing manufacturing costs and more stringent federal regulations, companies in the metal finishing industry are turning to “all-in-one” liquid additives for their chrome plating needs. By switching to a liquid form of chromic acid, you can make your facilities more productive and safer for your employees, while generating less waste at the same time.
It’s no secret that successful chrome plating has become increasingly difficult. Due to new rules from government agencies like the Occupational Safety and Health Administration (OSHA) and the Environmental Protection Agency (EPA), the regulatory environment surrounding this process has become even more stringent. Lower exposure limits for workers, hazardous waste regulations, and ongoing issues with uncertain futures regarding long-chain poly-fluorinated mist suppressants continue to make this process problematic to run both properly and within the regulatory guidelines. Technology advancements, like improvements in organic catalyst systems for hard chrome, have made the actual chemical process easier and more efficient, but complications still exist. Most chemical suppliers can provide products containing chromic acid which has already been dissolved in water. These are very concentrated solutions, usually 64oz./gal or more chromic acid, which will replenish the chrome concentration in your process tank without adding unnecessary volume, and can contain other additives like catalysts, saving you time and money.
The National Institute for Occupational Safety and Health (NIOSH) recommends that airborne exposure to all Cr(VI) compounds be limited to a concentration of 0.2 µg Cr(VI)/m3 for an 8-hr TWA exposure, during a 40 hour workweek. It can be difficult to keep your employees under this exposure level while the tank is performing normal plating operations. This is compounded when chemical additions are being made by dumping cans of chromic acid flake over the side. Solid chrome is traditionally very dusty and can become “chunky” if exposed to moisture. These chunks can fall into the tank and cause the solution to splash back onto the operator. Most companies do not have the engineering controls and rely on personal protective equipment (PPE) to properly use this material in their process. This can be a large liability because of the hazardous nature of this chemical.
There are many other benefits of using liquid chrome versus solid chrome, including when it comes to the ergonomic issue of employees lifting kegs of chrome, which often weigh over 50 lbs each. This can cause back issues from both the improper lifting of cans and the repetitive motions associated with lifting them. If a container is mishandled, it can be dropped and injure an employee by crushing their feet. When the material is being added into the tank, solution from the tank can also splash back and get into the operator’s eyes or on their skin or clothes, which can cause chemical burns and also expose them to higher levels of chromic acid than NIOSH recommends. When using liquid chrome, you can take the material right out of the hands of the operator with an automated addition system. This allows the operator to perform other tasks while the chromic acid is added to the bath via amp-hour meter. Process-wise, this makes the solution more stable and lowers part defects.
Waste is a serious factor that must be considered as part of the plating process. Leftover cans of chromic acid flake can create hazardous waste for the shop. These cans must be triple-rinsed before they can be disposed of, and they still must be considered to be hazardous waste. The drums and totes that contain the liquid chrome can be rinsed and disposed of through regular recycling programs. It is often easier to rinse and clean out the drums and totes than it is to rinse out the cans of solid flake for a variety of reasons, including size and quantity of the containers. This means a greater volume of water is often required to rinse out cans of solid flake.
The cost of using liquid material is typically thought to be more for obvious reasons; the extra labor and containers which are required for the solid chrome will understandably add to this, but we’ve found that the cost difference is actually smaller than one may think. The obstacles of filling a small steel can with chromic acid include but are not limited to the cost of the can, the labor to stack 18-36 heavy cans on a skid, the cost of the skid, banding materials, additional labels, etc. Along with the extra costs of the containers and labor, there are extra ventilation equipment and PPE required to handle chromic acid flake correctly, the potential costs of employee injuries and lost time due to improper handling, and the increased poundage of hazardous waste generated by using solid flake, the cost savings of switching to liquid products can add up to thousands of dollars per year.
Protecting the environment, your employees, and simplifying the plating process are just a few of the reasons you may want to consider switching to liquid chrome products. By switching to liquid chrome products, you can concentrate on what you do best: the plating.
Related Content
Automated Electroplating Systems
Simultaneous engineering reduces energy and resource consumption.
Read MoreProducts Finishing Reveals 2023 Qualifying Top Shops
Each year PF conducts its Top Shops Benchmarking Survey, offering shops a tool to better understand their overall performance in the industry. The program also recognizes shops that meet a set of criteria to qualify as Top Shops.
Read MoreIn-House Blackening of Ferrous and Non-Ferrous Metals
Process satisfies customers’ shipping requirements while meeting stricter water regulations in times of drought.
Read MoreChoosing and Troubleshooting Copper Electroplating Processes
Learn more on this inexpensive and highly efficient process.
Read MoreRead Next
Outside the Box Thinking on Passivation
Richard Held and Daniel Church of Haviland Enterprises Inc. offer advice for troubleshooting passivation inconsistencies.
Read MorePF Podcast Discusses CARB Hex Chrome Phase-out Deadlines
Products Finishing’s On the Line podcast discusses what recently proposed California hex chrome phase-outs may mean for metal finishers in the state and for the surface finishing industry at large.
Read MoreSwitching from Decorative Hexavalent Chromium to Trivalent
Pavco decorative team manager, Shane Moore, discusses the considerations you should keep in mind when contemplating switching from decorative hexavalent chromium to trivalent.
Read More