Torque Tension Modifiers
Matt Schario of Columbia Chemical discusses the principles of torque tension and why it is a concern for platers who coat fasteners.
Q. We plate for several OEMs and there seems to be a lot of focus on torque tension modifiers and the coefficient of friction ranges in various specifications. Can you help me understand the principles of torque tension and why it is such a concern?
A. This is an excellent question and one that others may appreciate you asking. Many applicators understand torque tension on a surface level but there are additional components to consider and having a deeper understanding of torque tension and what it impacts helps applicators know what to look for when meeting (or failing to meet) specs.
Every day and in nearly every aspect of our lives, people rely on the strength and performance of fasteners without giving them a second thought. But the manufacturers, engineers and applicators responsible for the fasteners that hold our world together give it plenty of thought. A critical component of this performance is torque tension.
At its most basic level, we know torque is a measurement of a force’s ability to cause an object to rotate. The harder you turn the wrench, the more torque you apply. This is known as input torque, or applied torque. Tension is the proper stretching of the bolt that provides the clamping force of the joint.
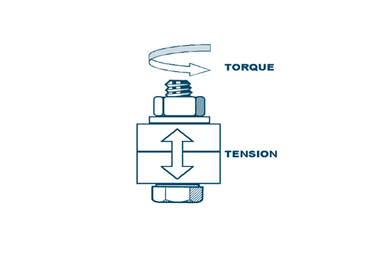
For OEMs and fastener manufacturers, torque tension is a major area of focus. The balance between torque and tension is delicate. If parts are insufficiently tightened, the bolts will come loose; if parts are over tightened, the bolts could break. Bolts must be stretched and stay stretched properly to avoid failure.
To address this critical component of fastener safety and technology, we often look to torque tension modifiers to help deliver greater precision. Torque tension modifiers are specialized additives developed to enhance the frictional characteristics between threaded fasteners and metal surfaces. By altering the coefficient of friction, or CoF, (the measurement of friction between the surfaces), torque tension modifiers facilitate more accurate torque-tension relationships during the fastening process. This plays an important role in achieving consistent and reliable clamp loads and torque control, which is crucial for ensuring secure connections and helping to prevent loosening, leakage and premature failure of assemblies.
Because the torque tension relationship and coefficient of friction are aligned in their critical role in fastener performance and safety, torque tension testing is an important component in both the development of the chemistry as well as in its application and overall compliance with OEM specifications. The goal of torque tension testing is to determine the coefficient of friction and torque values at a given clamp load with defined bolt, washer and nut dimensions.
There are three measurements related to friction coefficients. The first is the total friction coefficient which describes the overall friction that takes both thread and under head friction values into account. The second type is under head friction coefficient which describes friction between the bolt bearing surface and test plate or washer. The third is the thread friction coefficient which describes friction between mated threads.
The effectiveness of torque tension modifiers stems from their ability to modify the surface properties of the metal substrates. These modifiers typically contain lubricating or friction-enhancing agents that interact with the surface roughness and chemistry of the metal. It is important to note that not all torque tension modifiers are created equal. There are different types of torque tension additives used for various alloys and substrates. A modifier designed for zinc will not perform or provide the same coefficient of friction for zinc-nickel or tin zinc. Each can perform differently in areas of lubricity, corrosion protection, porosity, coefficient of friction, etc., so it is critical to use a torque tension modifier designed to work specifically with the coating you are applying it over to ensure you are meeting the requirements of your specification. The coefficient of friction needs can vary based on the coating, the substrate, the end use and the OEM specification.
It is important to work with a knowledgeable chemistry supplier when selecting the proper torque tension modifier for your application as there are some critical variables (spin speed, lubricant concentration, underlying plating and passivate layer, etc.) which can impact your results. Discussing your substrate, process sequence, operating parameters, and spec requirements will be key to achieving the proper CoF range. By understanding the relationship between torque, tension and the critical function torque tension modifiers can provide with respect to friction coefficients across different substrates, applicators can better ensure improved reliability and adherence to important performance specs.
About the Author
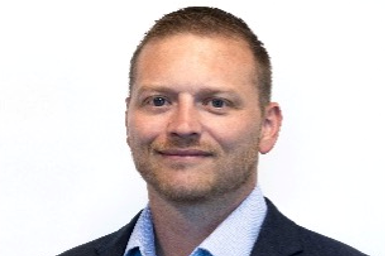
Matt Schario
Matt Schario serves as Director, Technical Service, at Columbia Chemical. For more info, visit columbiachemical.com
Related Content
Nickel Electroplating
Applications, plating solutions, brighteners, good operating practices and troubleshooting.
Read MoreGlass Bead Blasting as Plating Pretreatment
What are the best practices for using blasting in preparation for plating? Angelo Magrone of Bales Metal Surface Solutions discusses the ins and outs of glass bead blasting.
Read More3 Tests to Ensure Parts are Clean Prior to Plating
Making sure that all of the pre-processing fluids are removed prior to plating is not as simple as it seems. Rich Held of Haviland Products outlines three tests that can help verify that your parts are clean.
Read MoreRead Next
The 2024 Ford Mustang: All the Colors Available
Although Chevrolet has announced the end of the Camaro and Dodge is offering “Last Call” editions of the Charger and Challenger, the Ford Mustang is launching to its seventh generation.
Read MorePowder Coating 4.0: Smarter, Faster, More Efficient and Connected
New tools reduce cost and waste, lower manufacturing footprint of powder coating operations.
Read MoreEpisode 42: An Interview with Robin Deal, Hubbard-Hall
Hubbard-Hall wastewater treatment specialist Robin Deal discusses the latest trends in wastewater management.
Read More