Estimating the Electrocoat Usage of a Part
If you work at a job shop and would like to accurately estimate costs when quoting new business, Axalta’s Joe Subda has some great formulas to use.
Q: How can I estimate the electrocoat usage of a part? I work at a job shop and would like to accurately estimate costs when quoting new business.
A: Electrocoat usage per part is usually determined by multiplying the square foot of a part by the ecoat usage per square foot. The square footage should be supplied by the part manufacturer. The ecoat usage per square foot can be determined by two different methods — average and theoretical.
The average ecoat usage per square foot can be calculated by totaling the amount of paint used and dividing it by the square footage produced. Calculating paint per square foot using this method is accurate if the film build is the same throughout the part and from part to part.
An example of calculating the average ecoat usage per square foot — a line produces 8,000,000 square feet of metal a month, the resin usage is 11,000 gallons, and the pigment usage is 1,400 gallons. Therefore, (11,000 + 1,4000) / 8,000,000 = 0.00155 gallons/square foot.
Theoretical usage can be determined using the following formula. Please note this formula can be used for almost any liquid coating:
One square foot is equal to 144 square inches. One mil is equal to 0.001 inches. The factor 231 is the number of cubic inches in a gallon. Percent volume solids are the amount of paint per unit volume that can be applied to a part. Percent volume solids are not the same as percent weight solids. Percent weight solids are the amount of paint per unit weight that is nonvolatile. Percent volume solids are available from the paint suppliers. Losses are paint that is carried out of the tank but not part of the final coating. System losses and paint bake-off losses are the two biggest losses in an ecoat system. System losses are generally paint that goes down the drain in the final DI/RO rinse. The paint supplier can supply the paint bake-off losses and help determine the amount of paint that goes to drain in the final DI/RO rinse.
Here’s an example of calculating the theoretical ecoat usage of a part that is 100 square feet. The system loss is three percent, the bake-off loss is five percent, the volume solids are 30 percent and the film thickness is 0.7 mils.
Q: How do I calculate the amount of paint that is going down the drain in my final DIW rinse?
A: The following formula can be used to calculate cost of ecoat going to drain.
8.33 x DI Water Rinse rate x Solids to Drain x 60 minutes/hour x electrocoat cost/pound
8.33 is the weight of water. DI water rinse rate is the amount of fresh DI water used in the last DI rinse. Solids to drain is the percent nonvolatile of the solution going to the drain from the final DI rinse. E-Coat cost/pound can be determined using the following formula.

The pounds of resin solids can be calculated by multiplying the percent nonvolatile of the resin by the weight per gallon of the resin. The pounds of pigment solids can be calculated using the same formula just remember to substitute the pigment values for the resin values.
An example of calculating the e-coat cost/pound: resin cost is $10/gallon. Pigment cost is $15/gallon. The feed ratio is 8-to-1. The resin non-volatile is 40 percent and the weight per gallon is 9 pounds. The pigment nonvolatile is 60 percent and the weight per gallon is 12.5 pounds.
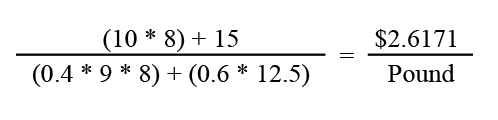
An example of calculating the cost to drain of the final DI rinse: the percent non-volatile of the solution going to drain is 0.1 percent. The DI water rinse rate is 10 gallons a minute. The e-coat cost/pound is $2.6171
- 8.33 ×x 10 ×x 0.001 ×x 60 ×x 2.6171 = $13.08/Hour
Ecoat is going down the drain at a rate of $13.08 an hour. That would be $52,320 a year for a two-shift plant working 50 weeks per year.
Q: How do you determine if there is enough anode area in my ecoat tank? I have a continuous conveyor system that runs at 20 racks an hour.
A: The following formula can be used to calculate square feet of anode required for a continuous conveyor system. Please note that the maximum square footage per rack will be needed to calculate required anode area.

An example of calculating anode area: maximum square footage per rack is 400. The racks are 20 per hour.

Related Content
Ecoat — An Entrepreneurial Approach
Job shop style approach for a captive ecoat line encourages ownership, innovation.
Read MoreCoatings Plant Evolves with Market Trends
Expanding its focus from exclusively serving the RV industry, one of this company’s stand-alone coatings plant has successfully extended its services to additional markets.
Read MoreECOAT24 Attracts Both Serious Electrocoaters and Novices Alike
The conference, held April 2-4, 2024, in Orlando, Florida, provides the ecoating industry with educational sessions, supplier exhibits and networking with colleagues.
Read MoreFinishing Systems Provider Celebrates 150 Years, Looks to Future
From humble beginnings as an Indiana-based tin shop, Koch Finishing Systems has evolved into one of the most trusted finishing equipment providers in the industry.
Read MoreRead Next
The 2024 Ford Mustang: All the Colors Available
Although Chevrolet has announced the end of the Camaro and Dodge is offering “Last Call” editions of the Charger and Challenger, the Ford Mustang is launching to its seventh generation.
Read MoreEpisode 42: An Interview with Robin Deal, Hubbard-Hall
Hubbard-Hall wastewater treatment specialist Robin Deal discusses the latest trends in wastewater management.
Read MorePowder Coating 4.0: Smarter, Faster, More Efficient and Connected
New tools reduce cost and waste, lower manufacturing footprint of powder coating operations.
Read More