3 Tests to Ensure Parts are Clean Prior to Plating
Making sure that all of the pre-processing fluids are removed prior to plating is not as simple as it seems. Rich Held of Haviland Products outlines three tests that can help verify that your parts are clean.
#asktheexpert
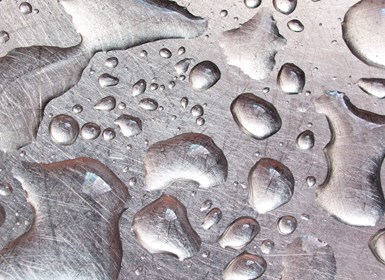
Q. I’m having issues with adhesion and patterns on my parts. I believe there might be an issue with my cleaners. How can I verify if they are working effectively?
A. Making sure that all of the pre-processing fluids are removed prior to plating is not as simple as it seems. For this question, I will assume that you have chosen the proper cleaner for the type of soils that you encounter on your parts. To verify that your cleaners are still working effectively, you can perform 3 quick tests.
Featured Content
1. White Glove Test
The simplest test is the “white glove” test. Using a clean rag or white glove, wipe the surface of the part after it comes out of your cleaning process and look for evidence of soils remaining on the cloth. Effective cleaners will leave behind no residue or residual oils. This test won’t work well for parts with small holes or welds that you can’t quite get the cloth into.
2. Water Break Test
The second test is called the “water break” test. After a part has been cleaned and dipped in an acidic rinse, the water from the rinse should “sheet” off of the part and not show any signs of beading or water break. This has been a long-used and reliable test for many and is good for testing parts on-line. Again, this isn’t as effective with small parts, or parts covered with water-soluble oils or other hydrophilic compounds that do not cause water break but still have negative effects on the surface.
3. Copper Sulfate Immersion Test
The final, and most effective, method is the copper sulfate immersion test. By utilizing the redox potentials of the copper and the iron, we are able to create an “immersion” layer onto the surface because, as the iron loses electrons into the solution, they are picked up by the copper and it is deposited onto the surface. This reaction can be further explained by reviewing the reduction potential of the two half-reactions below:
Cu+2(aq) + 2e- → Cu(s) E = 0.337V
Fe(s) → Fe+2(aq) + 2e- E = 0.440V
Fe(s) + Cu+2(aq) → Fe+2(aq) + Cu(s) E = 0.777V
To perform this test, immerse a part in a solution containing 16 g/L copper sulfate dissolved in water for 5 minutes. Rinse, dry and observe for patterns in the deposit or any loss of adhesion. If you see any patterns or areas where the copper does not adhere, then the part is still not clean and adjustments should be made to the cleaners.
Cleaners are a vital, but often overlooked, process component. Work with your chemical supplier to implement any process control tips they may have and periodically perform the tests described above and you will be well on your way to producing great looking parts.
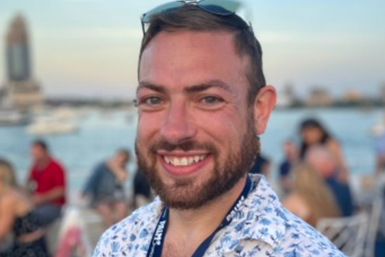
Rich Held is director of sales for Haviland Products Co. Visit havilandusa.com.
RELATED CONTENT
-
Plating with Zinc-Nickel: Benefits and Challenges
Chad Murphy of Columbia Chemical speaks about the benefits of various types of zinc-nickel alloy, and provides tips for manufacturers about the zinc-nickel plating process.
-
What Causes Discoloration of Clear Coat Powder?
Coaters sometimes have problems with cloudy appearance or yellowing of the coating, and expert Rodger Talbert has a few possible solutions.
-
Blistering Defects and How to Avoid Them
Verney Denerville of TIGER Drylac discusses recommendations for avoiding or mitigating blistering defects in powder coatings.