Filter Press Troubleshooting and Optimization
Zachary Beckman of Haviland Enterprises Inc. discusses proper filter press maintenance for optimization of wastewater treatment systems.
#asktheexpert #pollutioncontrol
Q: We have recently noticed our plate and frame filter press cake is no longer pressing properly and we are getting soupy and sticky sludge instead of the normal dry hard filter cake we are used to. What could be causing this issue and how can this be corrected?
A: When it comes to dewatering solids from wastewater treatment systems, a plate and frame filter press is reliable and is easily operated. However, changes in water chemistry or a lack of maintenance can quickly turn a filter press into a frustrating issue. The resulting soupy or sticky sludge that has not been properly dewatered will increase cycle time, causing a backup of solids in your system. This issue can even create problems with waste disposal vendors and cause the need for recharacterization if not resolved in a timely manner. A few of the most common causes of this are a lack of filter cloth maintenance, feed pump issues, poorly optimized coagulant use, and proper dosage of flocculants.
Featured Content
Filter Cloth Maintenance: Over time, your filter cloths can build up organic contaminants, precipitated metals, and excess flocculant polymer. Fouling of the cloths causes the efficiency of the press to be reduced and increasing the amount of time for a proper press cycle.
A few methods can be used to clean the filter plates and cloths including washing with a dilute cleaning solution, acid washing with dilute hydrochloric, power washing the cloths or any combination of these methods. Each of these methods has their advantages and drawbacks and should be reviewed to address what is fouling your cloths.
One of the simplest methods is to use a low-pressure spray (with or without a dilute cleaning solution). This type of wash can help remove some oils and organics, but it will not solubilize metals or most flocculants, leading to a secondary dilute acid wash being required.
An acid wash is generally effective in removing most materials from filter cloth pores. A cleaning solution can generally be run through a press (25% HCl) easily with a clean in place (CIP) system. Alternatively, you can set up a tank to soak the filter plates in dilute acid, but this will increase the amount of handling and the overall cleaning time. Plate/cloths are usually soaked overnight in a solution of 4-5% HCl. One will need a method to rinse the plates after soaking and consequently the added handling of spent cleaning solution. It is important to remember that when performing an acid clean, you will need to pay attention to acid compatibility with your filter press pump. If incompatible, use a different pump to move the solution through the filter press. For example, a cast-iron cased air-operated diaphragm pump is commonly found as a feed pump on filter presses and is not compatible with hydrochloric acid.
Power washing with hot or cold-water filter cloths is another option that can be alternated with one of the chemical methods. Care should be taken to prevent damage to the cloths. If too much pressure is applied to a small area the cloth can tear, rendering that filter plate inoperable. Additional personal protective equipment for employees may also be necessary due to the particulate and chemical constituents coming off the filter cloths.
The best solution will likely be a mix of the above methods and should be scheduled on a preventative basis. The proper cleaning of filter cloths will prolong the need for replacement, but eventually, filter cloths will need to be changed due to the wear and tear they experience.
Feed Pump Issues: When experiencing long cycle times, one should look to their feed pump. Air-operated diaphragm feed pumps can become partially blocked by debris and not allow the full feed pressure to the press. This is less common but can be cleared by disassembling the pump and clearing any debris. While disassembling the pump, it is important to check the diaphragms for holes or wear due to debris, as a hole in a diaphragm will cause the same issue, and over longer periods of time, diaphragms are a wearable part that needs to be replaced as needed.
Coagulant Optimization: Coagulant optimization can often be overlooked, especially if your wastewater system discharge water is meeting all permit requirements. If you are not feeding a coagulant, one might be required to condition your water and allow for better flocculant formation. Poor charge neutralization or a failure to treat organic contaminants will yield sludge that will not readily dewater and/or will clog your filter cloths. If you have a sludge that has never really pressed into a good solid cake, this might also be a sign a change to the coagulant dosage or type is needed. Coagulants that are organic in nature can fail to deal with some contaminants and inorganic salt-based coagulants can cause excessive sludge. Blended coagulants help bridge these problems but should be bench tested to determine the proper feed and type to maintain both permit limits and sludge dewatering. Any time a stream feeding the wastewater system changes, a coagulant review will be required for the application. Be especially mindful of production cleaner changes or any influx of oils or grease. In the case of heavy oils, a precoat of diatomaceous earth or lime will be needed for the filter cloths.
Flocculant Optimization: An overdose of flocculant or an improperly made down flocculant can cause the filter cake and filter press cloths to be sticky and slimy. When this happens, the press often needs to be acid washed to break down the flocculant polymer and open the pores in the filter press cloth. It is easy to accidentally overdose your flocculant. This can be caused by a drop in the total suspended solids feeding the system or a change in the flow rate of the system without proper adjustment of the polymer. Another issue commonly witnessed is poor flocculant make-down. For example, if making down your flocculant from a powder into a tank if the polymer is added to quickly or in slugs you can form polymer balls (fisheyes). These will not react with coagulated solids and will ultimately end up in the filter press, sliming up the cloths. This can be fixed by closely monitoring the addition or installing a screen ahead of the polymer feed pump. A simple option is to change to a version that is already made down into a liquid. This will prevent the risk of fisheyes and simplify the system for operators.
No matter what the cause, a poor filter cake can lead to large amounts of time troubleshooting the issue and unnecessary costs in fixing the issue along with disposal costs due to waste vendor issues. With the proper guide or help from an expert, this process can be resolved in a timely manner with little system downtime due to unplanned shutdowns.
About the Author
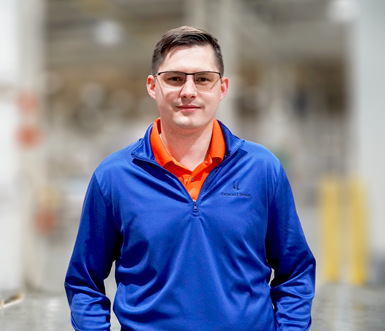
Beckman
Photo Credit: Haviland
Zachary Beckman
Zachary Beckman is an environmental engineer for Haviland Enterprises Inc. Visit havilandusa.com.
RELATED CONTENT
-
Cyanide Destruction: A New Look at an Age-Old Problem
Cyanide in mining and industrial wastewaters has been around from the beginning, including electroplating processes. This presentation reviews a number of current processes, and in particular, offers new technologies for improvement in cyanide destruction by the most common process, using sodium hypochlorite.
-
Is Your Electroplating Waste Hazardous?
Some that bears precious metals is, and there are a host of regulations to consider when recycling.
-
Treating Plating Wastewater
Wastewater from plating facilities contains contaminants such as heavy metals, oil and grease and suspended solids at levels that might be considered environmentally hazardous . . .