New replacement solvents excel for medical, aerospace, military, defense, automotive, and other precision/critical cleaning applications where the final product must be residue-free and applications where water will not work or is not desired. Photo Credits: Kyzen Corp.
Modern solvent cleaning systems are an efficient and safe way of performing cleaning while ensuring environmental health and safety (EH&S) compliance. However, numerous changes to the solvent cleaning market over recent years are now affecting end users. As some older-generation solvents are under review by the Environmental Protection Agency (EPA), Occupational Safety and Health Administration (OSHA), other health and environmental organizations as well as internal corporate EH&S bodies, solvents that are currently being used in a cleaning process may soon become unavailable because of the potential discontinuation by OEMs or phase-outs of these solvents by federal or state laws.
Finding and switching to a new solution is crucial for those who use solvent by choice or necessity. While this task may appear daunting to many, it is reassuring that alternative solutions are available. The question to ask in this case is, “How do I future-proof my choices?”
Featured Content
It is important to evaluate the viability of replacement solvents, and technical experts are available to assist with the evaluation process. Each solvent has its own characteristics, such as flammability, global warming potential (GWP), ozone depletion potential (ODP), occupational exposure limits (OEL), volatile organic compounds (VOC) classification, and other criteria to meet EPA/OSHA/end-user internal standards.
Chlorinated and brominated solvents
Older-generation solvents such as trichloroethylene (TCE), tetrachloroethylene (PCE), methylene chloride (MC), N-propyl bromide (nPB), and N-methylpyrrolidone (NMP) have been identified under the Toxic Substance Control Act (TSCA) for chemical risk analysis. There are many public documents from governing bodies that notify users of the risks involved with these solvents. More strict regulations for personnel exposure have been proposed and await enactment. The latest news about TCE is the EPA announcing a proposal to ban all uses of the solvent, which the agency describes as an extremely toxic chemical known to cause serious health risks including cancer, neurotoxicity and reproductive toxicity.
HFE and HFC solvents
With the decline of chlorinated and brominated solvents because of regulatory issues, the solvents of choice were fluorinated solvents and trans-dichloroethylene (t-DCE) blends. Common fluorinated solvent ingredients are hydrofluoroethers (HFEs) and hydrofluorocarbons (HFCs). These solvents provided acceptable cleaning results and improved EH&S properties over the older-generation solvents. However, they have recently been identified as creating environmental issues. These issues are global warming and per- and polyfluoroalkyl substances (PFAS) classification.
Based on this discovery, there are changes on the horizon for HFEs and HFCs. For instance, 3M announced it will exit PFAS manufacturing and work to discontinue the use of PFAS across its product portfolio by the end of 2025. The discontinued products include the company’s Novec solvents (HFEs).
Also, the EPA announced a framework to prevent new or foreign-sourced PFAS from entering the U.S. market without scrutiny. Therefore, HFC solvents will no longer be acceptable for use per Department of Defense (DoD), General Services Administration (GSA), and National Aeronautics and Space Administration (NASA) guidelines.
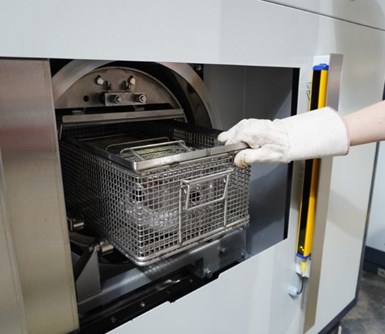
Modern, fully enclosed cleaning systems are an efficient and safe way of performing cleaning while ensuring EH&S compliance. Vacuum degreasing solvents were developed for operation under vacuum conditions in modern equipment to remove polar and nonpolar-based soils for a wide variety of manufacturing purposes.
The American Innovation and Manufacturing (AIM) Act enacted in December 2020 mandates a phase-down schedule of HFC production and imports through 2036 from baseline years 2011-2013. Beginning in 2024, 40% of HFCs will be removed from the marketplace, while by 2036, 85% of HFCs will be removed. Therefore, one can rule out future sustainability use with these solvents.
At this point, it is wise to determine if the solvent implemented in an application contains any HFEs or HFCs and then decide how to replace these solvents with safer options.
The quickest way to review the safety data sheet for a solvent is in Section 3: Composition/Information. This section contains information on the ingredients. However, proprietary ingredients may not be listed. If there are questions about a product, contact the solvent supplier for more information.
Next-generation solvents have superior EH&S features while offering similar operational performance as compared to other solvents. Newer generation solvents offer sustainable cleaning for the solvent user needing a viable replacement.
In most cases, the conversion to a next-generation solvent is simple and quick. Most of these solvents are designed as drop-in replacements in modern generation, open-top degreasers.
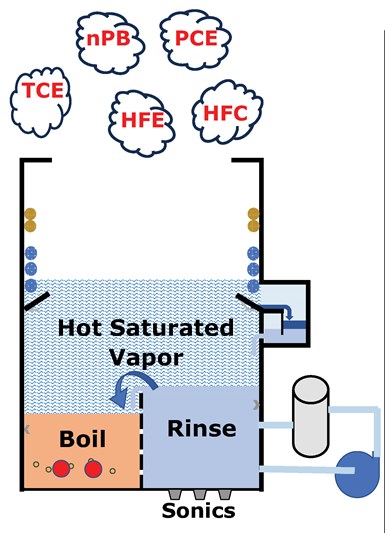
Because of the discontinuation of some solvents used in open-top vapor degreasers by the original manufacturer or phase out by federal and/or state regulatory agencies, these changes will require a replacement action to validate conversion results from several different aspects.
These new solvents are:
- Free from HFEs and HFCs
- Not classified as a PFAS by the EPA
- Non-flammable
- Non-ozone depleting
- Not classified as HAPs by the EPA
- Do not contribute to global warming
- Some are VOC exempt
- Most are compatible with a variety of metals and some plastic substrates
- Most operate from 120°F to 130°F
Listed below is a suggested matrix to assist in identifying the solvent to be replaced. Process evaluation is critical for success.
- Identify potential replacement candidates.
- Confirm “green” properties and regulatory approvals.
- Match performance to production requirements.
- Evaluate long-term future sustainability.
- Determine true operational cost of each candidate.
- Confirm local regulatory compliance.
- Implement conversion.
The vacuum degreasing solution
For the production process that requires solvent, vacuum degreasing offers sustainable cleaning options that are not only a viable replacement, but the solvents they use will help future-proof cleaning operations.
Depending on the soil type and loading, modified alcohols and non-halogenated hydrocarbons offer cleaning performance with desired environmental compliance. They not only ensure dependable, efficient and sustainable removal of oils, coolants and solids, but also enable cleaning and a corrosion protection process (if required) in one machine.
Modern, fully enclosed cleaning systems are an efficient and safe way of performing cleaning while ensuring EH&S compliance. Vacuum degreasing solvents were developed for operation under vacuum conditions in modern equipment to remove polar- and nonpolar-based soils for a variety of manufacturing purposes.
Implementing the vacuum degreasing cleaning method and its solvents have many other benefits such as:
- Compatibility with a variety of materials. Unlike aqueous detergents, vacuum degreasing solvents are non-corrosive, do not cause oxidation, discoloration or other surface impairments for most metals and some plastics.
- Excellent degreasing performance. Low surface tension combined with the solvency power of these solvents creates soil removal effectiveness without leaving residues on the parts.
- Rapid parts drying. Evaporative properties of the solvent in a heated, vacuum-sealed chamber enable parts to dry completely, removing solvent from blind holes and hidden passageways. This process eliminates solvent carry-out.
- Low solvent consumption. Soils are automatically separated from the solvent inside the vacuum degreaser because of the distillation process. The reclaimed solvent is returned to the process tanks for consecutive cleaning cycles. Thus, the solvent life is extended for an indefinite period.
- Solvent stability. Does not turn acid like some other industrial solvents. Any acid formation is because of the sulfonated/chlorinated oils/coolants being removed and is easily monitored and controlled.
- Low toxicity and eco-friendly operation. These solvents are not listed as hazardous air pollutants (HAPs) under EPA guidelines. The allowable operator exposure limits (OEL) are much higher than traditional vapor degreasing solvents. Continuous vacuum operation minimizes worker exposure.
- ASTM compliance. Modified alcohol has been certified for specific metals/tests.
- In-vitro cytotoxicity (medical). Modified alcohol has proven compliant to ISO 10993-5.
- Low VOC emissions. These chemical cleaning products, in combination with current vacuum degreasing technology and equipment, produce extremely low VOC emissions and find extensive use in California and other areas with demanding VOC requirements.
About the Author
Joe McChesney is the global product line manager – solvents for Kyzen Corp. Over 40 years of experience regarding solvent and aqueous cleaning processes from conceptual design through field operation. Contact: joe_mcchesney@kyzen.com
RELATED CONTENT
-
3 Reasons to Implement Vacuum Degreasing
Improvements in air emissions and waste when using vacuum degreasing also result in cost reduction.
-
Cleaning Limescale from Galvanized Steel
How do you clean white lime scale and rust spots on galvanize?
-
Cleaning Magnesium
Question: What is the recommended chemical cleaning process and composition prior to electroless nickel plating for magnesium?