NASF/AESF Foundation Research Project #122: Electrochemical Approaches to Treatment of PFAS in Plating Wastewater - 10th Quarterly Report
The NASF-AESF Foundation Research Board selected a project addressing the problem of PFAS and related chemicals in plating wastewater streams. This report covers the 10th quarter of work (April-June 2023). Here, we examine the effect of surface fluorination of Ti4O7 anodes on PFAS degradation performance in terms of energy performance as well as formation of chlorate and perchlorate when chloride is present in the solution. The full paper on this work can be accessed and printed at short.pfonline.com/NASF24Feb2.
#pollution control #energy #nasf
by
Qingguo (Jack) Huang* and Yuqing Ji
College of Agricultural and Environmental Science
University of Georgia
Griffin, GA, USA
Editor’s Note: The NASF-AESF Foundation Research Board selected a project addressing the problem of PFAS and related chemicals in plating wastewater streams. This report covers the tenth quarter of work (April-June 2023). A printable PDF version of this report is available by clicking HERE.
Featured Content
1. Introduction
This project started in January 2021 with the goal of developing applicable electrochemical approaches to remove per- and polyfluoroalkyl substances (PFASs) present in plating wastewaters, including electrooxidation (EO) and electrocoagulation (EC). This project includes three research tasks that are designed to investigate EC, EO and EC-EO treatment train, respectively, designed to probe three hypotheses specified follows:
1) EC generates amorphous metal hydroxide flocs that can effectively adsorb PFASs in plating wastewater, which, through an appropriate treatment, can release PFASs into a concentrated solution.
2) EO enabled by a Magnéli phase Ti4O7 anode can be used to effectively destruct PFASs in plating wastewater.
3) The electrochemical treatment train comprised of EC and EO by Ti4O7 anode can remove and degrade PFASs in plating wastewater more efficiently than either process operated individually.
In our previous report, we described results on the performance of surface fluorinated Ti4O7 anodes on PFAS degradation in batch mode. By comparing the reaction rate constant and anodic potential in pristine Ti4O7 anodes and surface fluorinated Ti4O7, we suggested that the intrinsic reactivity of Ti4O7 anodes towards PFAS was reduced upon surface fluorination but compensated by the increase in anode effective electroactive surface area (EESA) from fluorination. In this quarterly report, we further examined the effect of surface fluorination of Ti4O7 anodes on PFAS degradation performance in terms of energy performance as well as formation of chlorate and perchlorate when chloride is present in the solution.
Figure 1 - EE/O in relation to the anodic potential for PFASs degradation during EO treatment in batch mode on pristine and surface fluorinated Ti4O7 anodes; initial PFAS concentration: 2 μM, supporting electrolyte: 100-mM Na2SO4 + 10-mM NaCl.
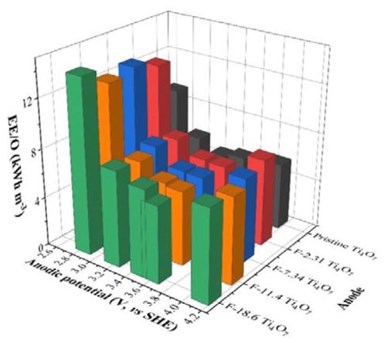
Figure 1 - EE/O in relation to the anodic potential for PFASs degradation during EO treatment in batch mode on pristine and surface fluorinated Ti4O7 anodes; initial PFAS concentration: 2 μM, supporting electrolyte: 100-mM Na2SO4 + 10-mM NaCl.
2. Tests and results
Based on the measured reaction rate constants from our experiments illustrated in the last report, the electric energy required to reduce the concentration of target contaminant by one order of magnitude (EE/O) was calculated for each anode and plotted in Fig. 1. For all anodes, it follows a general trend that the EE/O first decreases with increasing anodic potential because of rising reaction rates, but then increases as more energy is wasted on water oxidation at higher anodic potential. The optimal range of the anodic potential appears to be 3.2 to 3.6 VSHE regarding the lowest EE/O. Surface fluorination of the anodes slightly increased the EE/O. The EE/O at 10 mA/cm2 were 5.09, 5.55, 5.84, 6.02 and 6.24 kWh/m3 for the pristine, F-2.31, F-7.34, F-11.4 and F-18.6 Ti4O7 anode, respectively.
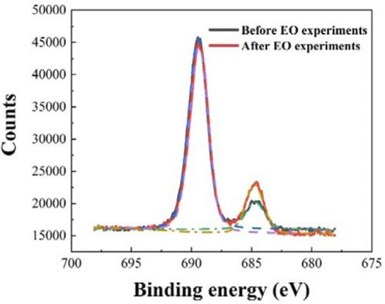
Figure 2 - The F 1s scan of F-18.6 Ti4O7 anode before and after the EO experiments.
After repeated EO experiments described above, XPS characterization was again performed on the F-18.6 Ti4O7 anode and compared to that collected before the EO experiment (shown in Fig. 2) to verify the stability of the anode surface fluorination. As seen in the figure, the total atomic percentage of F increased from 18.6% to 20.31% after the EO experiments. The CF3(-CF2-)n at the binding energy of 689.5 eV before and after the EO experiments did not change significantly (16.2% to 16.4%), indicating great stability on the anode, while Ti-F at the binding energy of 684.9 eV increased from 2.40% to 3.91%. This result may be due to the fluorine released from PFOA, PFOS and 6:2 FTS mineralization during EO binding to Ti on the Ti4O7 anode.1
Cl— can be oxidized to chlorate and perchlorate ions through a series of reactions, including DET and ·OH—mediated reactions during electrooxidation, initiated by the oxidation of Cl— to form Cl— on the anode.2,3 Formation of chlorate and perchlorate was observed during the EO treatments of PFASs shown in previous reports, as the testing solutions contained 10-mM NaCl. Figure 3 displays the time-course profiles of the chlorate and perchlorate concentrations during the EO treatment at 10 mA/cm2 with pristine and fluorinated Ti4O7 anodes, and their concentrations at the end of an 8-hr EO treatment at different anodic potentials are presented in Figure 4. It is evident in both figures that the formation of chlorate and perchlorate decreased with increasing surface fluorination.
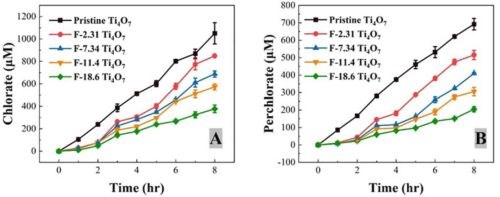
Figure 3 - The formation of (A) chlorate and (B) perchlorate during EO with pristine and fluorinated Ti4O7 anodes at 10 mA/cm2. The solution contained PFOA, PFOS and 6:2 FTS each at the initial concentration of 2.0 μM. Supporting electrolyte: 100-mM Na2SO4 + 10-mM NaCl. The error bar represents standard deviations of replicates.
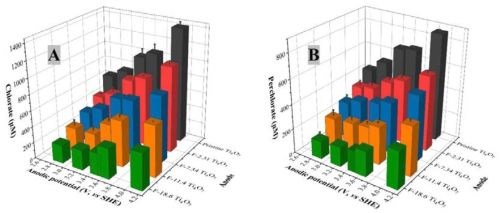
Figure 4 - The concentration of (A) chlorate and (B) perchlorate at different anodic potentials on pristine and fluorinated Ti4O7 anode after an 8-hr electrooxidation. Initial PFAS concentration: 2 μM, supporting electrolyte: 100-mM Na2SO4 + 10-mM NaCl. The error bar represents standard deviations of replicates.
3. References
1. Y. Wang, L. Li, Y. Wang, H. Shi, L. Wang and Q. Huang, “Electrooxidation of perfluorooctanesulfonic acid on porous Magnéli phase titanium suboxide anodes: Impact of porous structure and composition,” Chemical Engineering Journal, 431 (1), 133929 (2022).
2. Y.J. Jung, K.W. Baek, B.S. Oh and J-W. Kang, “An investigation of the formation of chlorate and perchlorate during electrolysis using Pt/Ti electrodes: The effects of pH and reactive oxygen species and the results of kinetic studies,” Water Research, 44 (18), 5345-5355 (2010).
3. A. Donaghue and B.P. Chaplin, “Effect of Select Organic Compounds on Perchlorate Formation at Boron-doped Diamond Film Anodes,” Environmental Science & Technology, 47 (21), 12391-12399 (2013).
4. Past project reports
1. Introduction to Project R-122: Summary: NASF Report in Products Finishing; NASF Surface Technology White Papers, 85 (6), 13 (March 2021); Full paper: http://short.pfonline.com/NASF21Mar1.
2. Quarter 1 (January-March 2021): Summary: NASF Report in Products Finishing; NASF Surface Technology White Papers, 85 (12), 13 (September 2021); Full paper: http://short.pfonline.com/NASF21Sep1.
3. Quarter 2 (April-June 2021): Summary: NASF Report in Products Finishing; NASF Surface Technology White Papers, 86 (3), 18 (December 2021); Full paper: http://short.pfonline.com/NASF21Dec2.
4. Quarter 3 (July-September 2021): Summary: NASF Report in Products Finishing; NASF Surface Technology White Papers, 86 (6), 16 (March 2022); Full paper: http://short.pfonline.com/NASF22Mar2.
5. Quarter 4 (October-December 2021): Summary: NASF Report in Products Finishing; NASF Surface Technology White Papers, 86 (9), 21 (June 2022); Full paper: http://short.pfonline.com/NASF22Jun2.
6. Quarter 5 (January-March 2022): Summary: NASF Report in Products Finishing; NASF Surface Technology White Papers, 86 (12), 22 (September 2022); Full paper: http://short.pfonline.com/NASF22Sep2.
7. Quarter 6 (April-June 2022): Summary: NASF Report in Products Finishing; NASF Surface Technology White Papers, 87 (3), 17 (December 2022); Full paper: http://short.pfonline.com/NASF22Dec1.
8. Quarter 7 (July-September 2022): Summary: NASF Report in Products Finishing; NASF Surface Technology White Papers, 87 (6), 19 (March 2023); Full paper: http://short.pfonline.com/NASF23Mar2.
9. Quarter 8 (October-December 2022): Summary: NASF Report in Products Finishing; NASF Surface Technology White Papers, 87 (9), 19 (June 2023); Full paper: http://short.pfonline.com/NASF23Jun1.
10. Quarter 9 (January-March 2023): Summary: NASF Report in Products Finishing; NASF Surface Technology White Papers, 87 (12), 17 (September 2023); Full paper: http://short.pfonline.com/NASF23Sep2
5. About the principal investigator

Qingguo (Jack) Huang is Professor in the Department of Crop and Soil Sciences, University of Georgia, Griffin Campus. He holds a B.S. in Environmental Science (1990) and a Ph.D. in Chemistry (1995) from Nanjing University, China as well as a Ph.D. in Environmenal Engineering from the University of Michigan, Ann Arbor, Michigan. Dr. Huang’s research interest focuses on catalysis involved in the environmental transformation of organic pollutants, and development of catalysis-based technology for pollution control and environmental remediation and management. His laboratory has been actively involved in several cutting-edge research topics:
- Enzyme-based technology for water/wastewater treatment and soil remediation
- Electrochemical and reactive electrochemical membrane processes in wastewater treatment
- Catalysis in biofuel production and agro-ecosystem management
- Environmental fate and destructive treatment methods of PFASs
- Environmental application and implication of nanomaterials
He has published over 170 peer-reviewed journal articles, five book chapters and had six patents awarded. He has taught three courses at the University Georgia: Introduction to Water Quality, Environmental Measurement and Advanced Instrumental Analysis in Environmental Studies.
* Principal Investigator (PI) Contact Information:
Qingguo Huang, Ph.D, Professor, Department of Crop and Soil Sciences,
University of Georgia, 1109 Experiment St., Griffin, GA 30215, USA.
Phone: 770-229-3302
Fax: 770-412-4734
E-mail: qhuang@uga.edu
RELATED CONTENT
-
Expanding on E-Coat
Electrocoat products and processes continue to evolve, with development focused on lower energy use, very low VOC content and methods to reduce cost per applied square foot. The following is a primer on how a combination of new materials and good process control can be used to achieve the highest possible efficiency.
-
Vanadate Conversion Coatings: Alternative to Phosphate?
Emerging pretreatment technology can reduce energy consumption and environmental concerns.
-
Electric vs. Pneumatic Agitators: What Makes Sense?
When determining the need for an agitator, says Mike Elberson from Autoquip, you must look at budget versus long-term energy conservation.