Powder Coating Aluminium Adhesion Failure
PF columnist Rodger Talbert offers advice for mitigating adhesion failure of powder coating on aluminum parts.
#asktheexpert
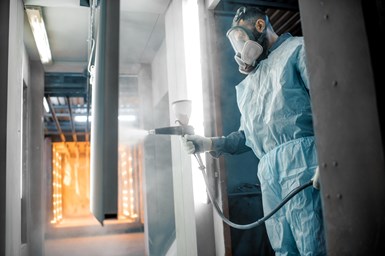
Q: We powder coat both aluminum and steel on the same line. We have a blast process with use for the steel and we have a 5-stage iron phosphate washer following the blaster. The product is bleacher seating so it must have good sunlight resistance as well as good corrosion resistance. We have had some problems with rust on the steel beams and some issues with adhesion failure of the powder on the aluminum parts. Can you evaluate our current process and suggest changes that will help us avoid these failures?
A: With a blaster and 5-stage washer, you should be getting a good coating on the steel beams. My suspicion is that the powder coating is not thick enough or coverage is incomplete. You should inspect steel carefully to see if the coating is light and thin in some areas. The most vulnerable areas are the edges and web of the beam. Sharp edges are hard to cover and often require a primer to ensure adequate coverage when the part is installed outside. The web area is rough, and the inside corner will have some electrostatic resistance, so coverage in that area may be light. Work on coverage and get a minimum of 3 mils on all surfaces.
Featured Content
As for the aluminum, your process is not conducive to good performance for outdoor use. You need an aluminum conversion coating to get the needed adhesion and longevity. A 4-stage washer with a good non-chrome aluminum treatment would be much better than iron phosphate, even if you are using fluoride in the current wash process.
If I had your system and parts, I would set up the washer for aluminum and use a good aluminum conversion coating. When you run steel turn off the washer and go with blast only. You will have to have a good blow-off to get rid of the residual blast media. You also must get the thickness of the coating up to ensure that you can avoid the rust issue. Make sure you are using a high-quality powder material that can add the needed protection.
Since your installations are outdoors and not easily repaired, you need to perform regular testing to make sure the process is producing the necessary quality. For the steel, you must check the film thickness constantly. Also, maintain regular corrosion testing using a cyclic process or salt spray to confirm consistent results. If you do not have this equipment, you can work with a lab to keep up the testing. This does cost some money, but I am sure it is cheaper than fixing field failures.
For the aluminum, run panels regularly and subject them to a wet adhesion test. Heat up demineralized water to a boil. Cut a cross-hatch pattern in the panel and immerse it in the heated water for 20 minutes. Do a tape pull test as outlined in ASTM D-3359. The entire process is described in AAMA (American Architectural Manufacturing Association) 2605. Do a panel with every shipment to be sure the aluminum is properly treated. If you pass the tape pull with no lift of powder, you should be good to go.
About the Author
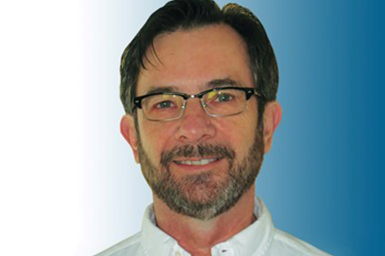
Rodger Talbert
Rodger Talbert has more than 30 years experience in the powder coating industry.
RELATED CONTENT
-
Top Reasons to Switch to a Better Cleaning Fluid
Venesia Hurtubise from MicroCare says switching to the new modern cleaning fluids will have a positive impact on your cleaning process.
-
Blistering Defects and How to Avoid Them
Verney Denerville of TIGER Drylac discusses recommendations for avoiding or mitigating blistering defects in powder coatings.
-
TGIC Powder Coatings vs. Non-TGIC Powder Coatings
As raw materials become increasingly scarce, powder coating consultant Rodger Talbert offers insights into using non-TGIC products.