
Berl Stein, founder and president of NiCoForm (Rochester, N.Y.), is the Rochester Section of the American Chemical Society’s 2020 Entrepreneur of the Year. This award recognizes Stein’s development of innovative chemistry for the highly precise fabrication of metal parts with superior mechanical and chemical properties using electroforming, and his foundation of NiCoForm in 1999 to commercialize this breakthrough additive manufacturing technology. The society will recognize Stein at its Annual Awards Dinner on a to-be-determined 2021 date. This award and Stein’s impressive technical and business achievements highlight the continuing central role of chemistry in economic development.
Berl Stein was born in Chernivtsi, Ukraine and received his B.S. and M.S. in chemical engineering from the Moscow Institute of Fine Chemical Technology. He began his industrial career in metal-plating technology in 1977 at ElectronMach before later working at metal fabricator LegMach. In 1988, Stein moved to the U.S. and began his work in the field of electroforming, first at Servometer Corp. (Cedar Grove, N.J.) and then in Rochester, New York at Reflexite Corp.

Cold shields, bellows and electroforms represent some of NiCoForm’s capabilities. Photo courtesy of NiCoForm
Stein founded NiCoForm in the spring of 1999 with a single hand-me-down tank. Today, NiCoForm consists of 22 employees and occupies a much larger manufacturing space, where it prepares precision metal parts for a broad spectrum of demanding markets. Stein attributes his company’s success to continually improving its chemical and processing technologies to meet the ever-evolving needs of his diverse customers, especially in critical medical, aerospace, optical and other high-tech applications.
Stein and his first employee originally offered selective metal plating services for mold repair, learning throughout NiCoForm’s early years as they battled alloy properties and adhesion issues. Armed with a small conventional lathe, a single plating tank and a drive to gain customers, Stein and his team stuffed envelopes soliciting customers to try NiCoForm’s molds for catheters. Eventually, catheter-tipping dies became the company’s bread and butter, and it formed them day-in and day-out.
Shortly after, NiCoForm added a focus on making bellows while Berl continued to develop and optimize the chemistry for a proprietary nickel-cobalt electroforming technology. The resulting process, which strengthens the nickel and uses custom additive manufacturing technology, created the NiColoy alloy that is now the core of NiCoForm’s growing business. Even after several expansions, including the addition of computer numerical control (CNC) machining, inspection, chemical laboratory and office divisions, NiCoForm continues to develop advanced electroforming techniques for customers throughout North America, Europe, Asia and the Middle East.
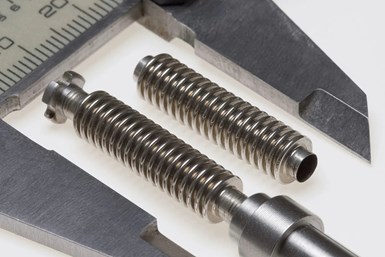
Electrojoining is an electroforming-based joining technique that permanently bonds two or more parts by an electroplated layer. Here, a small bellows is electrojoined to machined ends. Photo courtesy of NiCoForm
NiCoForm continues to innovate with high-performance electroformed seamless bellows; catheter tip-forming dies; optical and microfluidic mold inserts; and the cost-effective fabrication of precision metal parts for use in laser, aerospace, medical and many other applications. The company focuses on continually improving its chemical and fabrication technologies for applications where its high-strength proprietary alloy can provide the greatest benefit to its customers and their products. With a “world-class alloy” and a diverse customer portfolio, NiCoForm is reported to be a world leader in nickel-cobalt electroforming and an important part of Rochester’s high-tech chemistry-based industrial infrastructure.
NiCoForm’s Rochester facility is built around Berl’s non-polluting recuperative rinsing concept. This technique sends no plating chemicals down the drain, saving valuable materials while protecting the environment.
Related Content
How to Maximize Nickel Plating Performance
The advantages of boric acid-free nickel plating include allowing manufacturers who utilize nickel plating to keep up the ever-changing regulatory policies and support sustainability efforts.
Read MoreIn-House Blackening of Ferrous and Non-Ferrous Metals
Process satisfies customers’ shipping requirements while meeting stricter water regulations in times of drought.
Read MoreCleaning, Pretreatment to Meet Medical Specs ISO 13485 or FDA 21 CFR820
Maximilian Kessler from SurTec explains new practices for industrial parts cleaning, metal pretreatment and decorative electroplating in the medical device industry.
Read MoreFilter Press Troubleshooting and Optimization
Zachary Beckman of Haviland Enterprises Inc. discusses proper filter press maintenance for optimization of wastewater treatment systems.
Read MoreRead Next
Powder Coating 4.0: Smarter, Faster, More Efficient and Connected
New tools reduce cost and waste, lower manufacturing footprint of powder coating operations.
Read MoreEpisode 42: An Interview with Robin Deal, Hubbard-Hall
Hubbard-Hall wastewater treatment specialist Robin Deal discusses the latest trends in wastewater management.
Read MoreThe 2024 Ford Mustang: All the Colors Available
Although Chevrolet has announced the end of the Camaro and Dodge is offering “Last Call” editions of the Charger and Challenger, the Ford Mustang is launching to its seventh generation.
Read More