Solar-Powered Photonic Cooling Enables Energy-Saving Coating
Passive cooling technology can reduce interior temperatures 5-13°C, offering weight, cost and CO2 benefits for cars, construction, aircraft and more.
#energy #sustainability
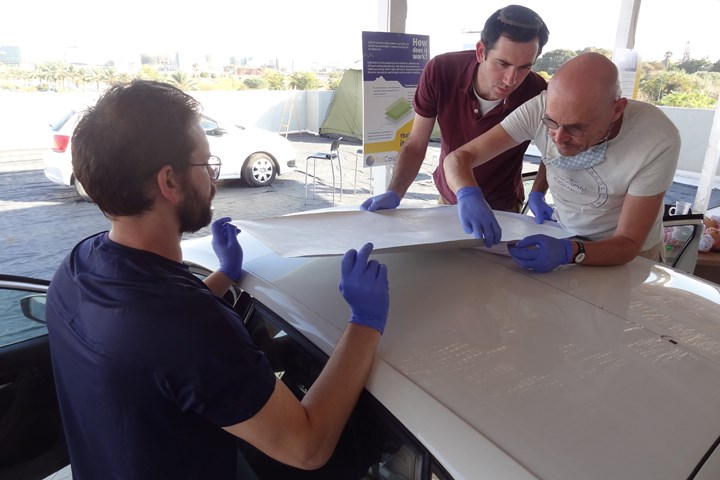
SolCold Glacier 110 film application to an automotive roof panel. Photo credit, all images: SolCold
The world just experienced its hottest June on record, and 2024 is projected to be even hotter. Cooling accounts for 10% of global electricity demand, which can rise by more than 50% in summer. If every 1°C increase in temperature above 24°C can drive a 4% rise in electricity demand, in Texas, for example — then what might be possible with every 1°C decrease if it was achieved by passive cooling, without electricity? An Israeli deep-tech startup known as SolCold (Ness Ziona) has been working on an innovative coating aimed to do just that — to cool the shell of a car, container, airplane or building by 5-12°C, reducing the need for air conditioning, its energy consumption and potential greenhouse gas emissions — using clever physics and the power of the sun.

SolCold’s technology is based on passive cooling, absorbing photons and then emitting thermal radiating, thereby transferring heat away from surfaces.
Passive cooling takes energy from the environment and converts that using physics — evaporation using water, for example, or blackbody radiation/infrared (IR) emissions — to transfer heat away from surfaces without using any power. Passive radiative cooling has been known for centuries and pursued in buildings for decades, but it’s challenging to achieve at the hottest times of the day because all natural materials absorb more solar energy than they can radiate — even the whitest paint. Founded in 2016 by Yaron Shenhav, Gadi Grottas and Guy Ron, SolCold launched its first product in 2021: a coating material that passively cools surfaces by reflecting sunlight and emitting thermal radiation, but going even further by using the photons that it does let through to reduce the energy in the atoms of the coating, effectively refrigerating it. Called Glacier 110, this coating film can be applied to a variety of surfaces, with the goal of reducing the need for energy-intensive air conditioning and improving energy efficiency.
Featured Content
How the technology works
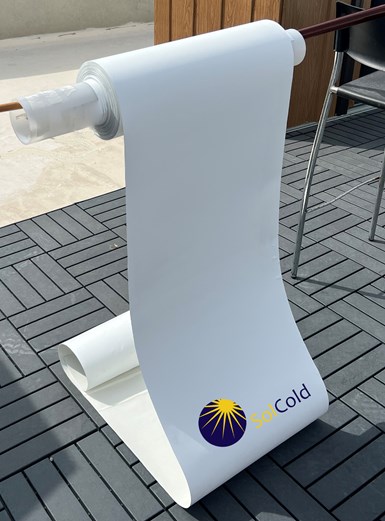
SolCold Glacier 110 film is available in 50-centimeter-wide rolls of varying lengths up to 50 meters.
Glacier 110 comprises a top layer that provides wear and abrasion resistance and also reflects 98.5% of solar radiation while amplifying “useful” wavelengths of light. Those useful photons are then absorbed by the next layer, which uses anti-Stokes fluorescence to emit photons back at a higher energy, lowering the energy within the material, and effectively achieving refrigeration. A subsequent radiative cooling layer further augments this cooling effect. The mirrorlike layer on the bottom, explains Shenhav, “is so that everything we are emitting in our upward converting of photon energy goes away from the substrate because we don’t want that to heat up.”
Glacier 110 is currently available as an adhesive film that can be cut to meet almost any shape and supplied in 50-centimeter-wide rolls. Length can vary, with the maximum being 50 meters, which primarily targets buildings and large structures. The technology offers potential for applications in a wide range of industries such as construction, transportation, agriculture, energy, communications, automotive and aerospace.
Glacier 110’s full daylight cooling power is 80-110 watts per square meter sub ambient. Thus, coating the top of a 20-foot shipping container (13.86 square meters) could rival the power of a small window air conditioner (5,000 BTU/hour where 1 watt=3.41 BTU). It does this at a thickness of 350 microns and an area density of 0.29-0.31 kilograms per square meter, weighing 300-400 grams per square meter. The cost of the film ranges from $65-120 per square meter, depending on needs and qualifications.
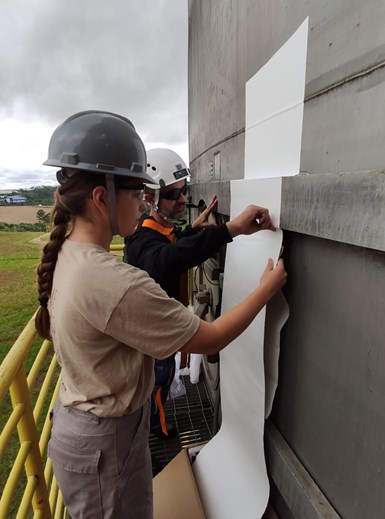
SolCold’s Glacier 110 film is said to yield a return on investment in cooling cost savings within 1.1 years and exhibits a life expectancy of more than 10 years in construction applications.
Current applications
A majority of SolCold’s success has been applying its film to metal substrates — it has been used for cars, electronic boxes, rooftops, warehouses and storage containers. The film can also be used for some plastics and composites, provided the substrate has good thermal conductivity. Any insulating particles on the surface can disrupt the efficiency in the cooling effect to the interior. In addition, the film also requires surface preparation of the substrate. The surface of the material must be smooth for the film to adhere.
SolCold has trialed Glacier 110 on car rooftops and is exploring use in vehicle interiors. When used in these applications, the technology helped to reduce cabin temperature by 9-12°C. Air conditioning consumption was also reduced by 30% and driving distance increased by 7%. Given concerns over range for electric vehicles, one can imagine the benefits of conserving the energy required to cool these types of vehicles.
Within the construction industry, Glacier 110 is said to yield a return on investment in cooling cost savings within 1.1 years and exhibits a life expectancy of more than 10 years. This offers advantages to building projects seeking Leadership in Energy and Environmental Design (LEED) certification, a globally accepted green building rating system.
Within the electronics industry, Glacier 110 is reported to reduce central processing unit (CPU) temperature by 5°C. According to SolCold, this can translate to up to 50% less maintenance, doubling mean time between failure (MTBF), a measurement of the average up-time of equipment between breakdowns or outages.
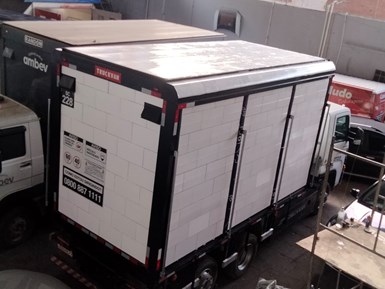
SolCold’s coating technology can increase passive cooling of refrigerated vehicles and shipping containers.
One particularly successful implementation of SolCold’s technology is in the shipping industry when a cold chain is required. A cold chain is a temperature-controlled supply chain comprising refrigerated production, storage and distribution facilities, supported by equipment that can constantly maintain the required low temperatures. Trucks or refrigerated shipping containers used in a cold chain often rely on a condensing unit, or compressor, and a refrigerant to condition the air and generate the necessary cooling. SolCold’s technology can increase passive cooling of vehicles and containers, enabling more efficient use or downsizing of compressors, reducing energy consumption and emissions. In addition, the use of Glacier 110 for the passive cooling of shipping containers can extend the time they can be unplugged from an energy source during layovers at ports or other transition points.
Potential applications
The need for increased cooling efficiency is becoming obvious with the growing development of alternative modes of propulsion. Electric power, whether supported by hydrogen fuel cells or batteries, means limited energy capacity. Every point where energy might be saved counts. As aerospace companies explore electric- or hydrogen-based propulsion methods, passive cooling technology such as SolCold’s film could be instrumental in helping conserve valuable energy, thus extending range and reducing carbon emissions.
In the meantime, SolCold is exploring ways to further improve its technology and extend it into a growing number of applications, including aerospace, as well as transportation and defense.
RELATED CONTENT
-
Rework and Recoating Powder
Powder coating rework requires more than just recoating the part. Products Finishing columnist and powder coating consultant Rodger Talbert discusses proper steps that should be taken to ensure a quality finish.
-
Powder Coatings vs Energy-Cure Coatings
Examining the basic differences between powder coatings and energy-cure coatings can help answer the question of whether or not one of these technologies might be appropriate for a specific application.
-
Powder Coating Week 2024 Offers Education and Networking
On March 11-13, 2024, this event for powder coaters will combine training, presentations, technical sessions, tabletop exhibits, roundtable discussions, expert panels and social activities.