Modular MOM System Bundles Functional Areas of Digital Factory
MOM System from Dürr and subsidiary iTac is a complete, single-source solution for production planning and control.
Edited by
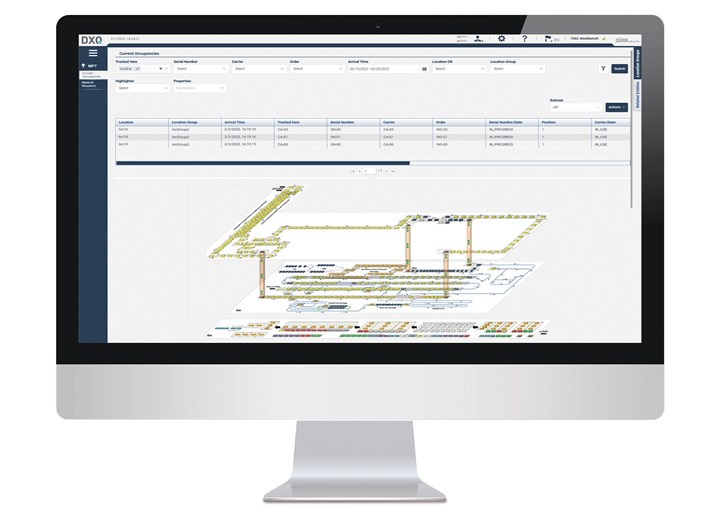
The modular micro-service architecture of the MOM system offers a variety of applications across the entire production. Shown here is the Material Flow Track application. Photo Credit: Dürr
Using its manufacturing and digitalization knowledge to combine hardware and software, Dürr’s software specialists and subsidiary iTAC developed a modular solution for manufacturing planning, execution, control, monitoring, optimization and predictive analysis. The Manufacturing Operations Management (MOM) system developed by the two companies relies on micro-services that provide functionality as required, instead of monolithic individual solutions. According to Dürr, the system enables a high level of flexibility and consistency, and offers many interfaces in terms of interoperability.
There are three central superordinate control components in a digital factory: a manufacturing execution system (MES) which controls and monitors production; supervisory control and data acquisition (SCADA) which collects and analyzes data; and a human machine interface (HMI) which visualizes production and process flow.
In the past, each of these components have mostly been designed as stand-alone solutions. For the MOM’s architecture, Dürr and iTac merged the functional scopes of MES, SCADA and HMI. This was made possible by combining Dürr’s DXQcontrol product family with iTac's iTac.MOM.Suite. As a result, manufacturing companies — whether producers or suppliers — receive an industrial digitalization solution with interoperable modules said to cover all smart factory functionalities.
With its modular structure, the architecture of the MOM’s multiple micro-services offers self-sufficient data storage and open interfaces for communication with other services for flexible deployment. Operation is made more sustainable by the installation of only necessary modules. The modular approach to the system is also said to make it less error prone, increasing plant availability.
Another advantage of the MOM’s micro-services is their flexibility with installation on IIoT platforms in the cloud, on site or in a hybrid factory. Customers can use specific cloud services while rolling out other functionalities on site if there are operating cost or production stability concerns, for example. The hybrid solution is noted to be advantageous for large data volumes in the terabyte range. Processing some of the data locally saves time, costs and energy as not all data sets have to be transferred to the platform through many transactions. In addition, local processing can offer the speed needed to control manufacturing processes in real time.
Dürr and iTac’s analysis tools utilize artificial intelligence to improve production quality and availability. They can act as MOM system components. The products evaluate production and quality data, using machine learning to make forecasts and also potentially detecting defects or impending wear. These prevention and prediction services, and the integration of edge technologies provide optimization, increased added value and data sovereignty, according to the company.
To make a smart factory a reality, machines and systems from all subareas must communicate with each other, and end-to-end digitalization must be achieved. Dürr and iTac’s MOM system aims to help digitize companies and open them to the possibilities a smart factory can offer.
Dürr | durr.com
RELATED CONTENT
-
Operations Software for Finishing Shops from Amariko
Amarikos’ PFC Shop Floor empowers finishing shops with touchscreen-based technology to improve production and quality.
-
Atotech Offers Specialty Chemicals, Technologies for Numerous End-Markets
Atotech, a leading specialty chemicals and technology company, delivers chemistry, equipment, software and service to support diverse end-markets such as automotive, EV battery, ConAg, energy, plumbing fixtures and more.
-
NADCAP Scanner Provides Fully Digital Production, Automated Certification Management
The scanner technology aims to minimize errors, inefficiencies and vulnerabilities that cause challenges for the industry.