Published
A Quantitative Test for Determining the Bond Strength Between an Electroplated Coating and the Basis Metal
One of the parameters describing the appropriate quality of electroplating is the bond strength between the plating and the basis metal. All other things being equal, corrosion protection of the basis metal is important, but the bond strength between the plated coating and the basis metal is absolutely critical.
by
V.V. Artamonov* and V.P. Artamonov.
The Pavlodar State University
Pavlodar, Kazakhstan
ABSTRACT
A simple and reliable method for the quantitative measurement of bond strength of an electroplated coating on a steel basis metal by means of an adhesive joint is suggested. The method can be used as an alternative to known ways of quantitative determination of the bond strength, and to standard methods, which assume only quality assessment of the bond strength.
Keywords: galvanic plating, electroplating, bond, steel basis metal, adhesive joint, break-off force.
Introduction
One of the parameters describing the appropriate quality of electroplating is the bond strength between the plating and the basis metal. All other things being equal, corrosion protection of the basis metal is important, but the bond strength between the plated coating and the basis metal is absolutely critical.
The control of the bond strength of metallic plating with the basis metal is carried out under the Russian Standard GOST 9.302-88.1 The ordered methods are based on the distinction of physicomechanical properties of the plated metal and those of the basis metal, the method of control chosen being dependent on the type of plating. However, the standard methods - polishing, scratch-brushing, bending, coiling, etc. - enable one to assess the adhesion strength only qualitatively, based on the presence or absence of blisters or peeling.1
At the same time, in some cases there is a need for a quantitative assessment of the bond strength. Such situations arise, for example, in the process of designing new electrolytes for electrodepositing this or that kind of galvanic plating. A new electrolyte may provide a stronger bond when compared with known electrolytes. However, this advantage can only be demonstrated by determining the quantitative bond strength.
There are a number of known methods used to determine the quantitative bond strength, usually involving the measurement of the force necessary to separate the coating from the basis metal.2 However, these methods have certain disadvantages, including the difficulty of manufacturing test samples. Further, thick coatings, not less than 300 μm, are required. Because of these requirements, the results do not related to practical usage.
Experimental procedure
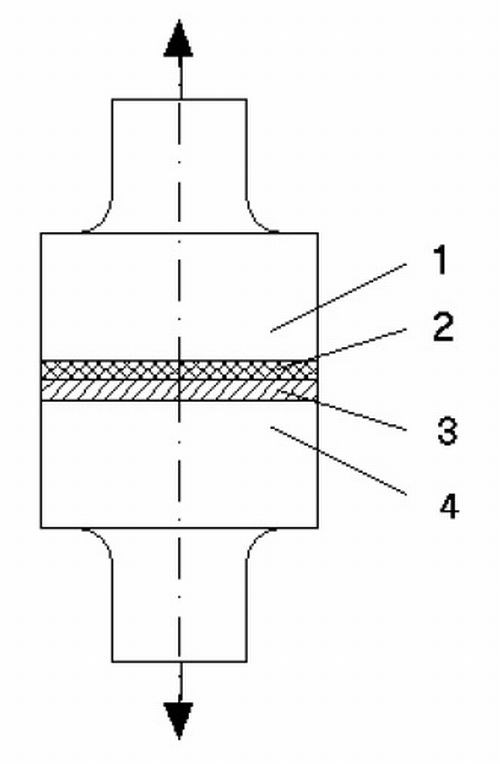
Figure 1 - Schematic diagram of tensile testing: (1 and 4) steel samples; (2) adhesive joint; (3) galvanic plating.
Our method for a quantitative determination of bond strength between an electroplated coating and a steel substrate is shown schematically in Fig. 1. Items (1) and (4) are test samples, consisting of chromium-molybdenum-vanadium alloy steel, and are cylindrical in shape. Their larger diameter is 25 mm and the smaller diameter is 6.0 mm. The smaller diameter sections are used to mount the device in a tensile test machine. The end surfaces of these pieces are polished. Initially, a plated layer (3) is electrodeposited onto the end of test sample (4), which is given a cold water rinse, followed by a hot water rinse, and then air dried. Next, a quick-drying cyanoacrylate glue (2) is applied to the end of test piece (1), and the test samples are joined. The adhesive joint is allowed to dry for 30 min in all experiments. After drying, the samples are fixed to the clamps in the test machine and the tensile test was carried out. The force required to separate the two test pieces (1 and 4) was measured.
Copper and zinc plating were used in this study. The electrolyte compositions used are given in Table 1.2 All experiments were performed at a current density of 1.0 A/dm2, an electrolyte temperature of 25°C and a plating time of 30 min. The chosen values of current density and time yield a plate thickness of 6.0 μm for both copper and zinc.
Table 1 - Composition of electrolytes used in this study.2
Electrolyte composition2 (g/L) | ||||
Electrolyte constituent | Bath No. 1: Sulfate Copper | Bath No. 2: Pyrophosphate Copper | Bath No. 3: Sulfate Zinc | Bath No. 4: Pyrophosphate Zinc |
CuSO4•5H2O | 200 | 90 | ---- | ---- |
H2SO4 | 75 | ---- | ---- | ---- |
К4Р2О7•3H2O | ---- | 370 | ---- | 300 |
ZnSO4•7H2O | ---- | ---- | 250 | 50 |
Al2(SO4)3•18H2O | ---- | ---- | 30 | ---- |
Na2SO4•10H2O | ---- | ---- | 50 | ---- |
Dextrin | ---- | ---- | 8 | 4 |
The cathodic polarization measurements were carried out with a potentiometer P-5827 in galvanodynamic mode at the given current sweep rate of 1.0 A/min. The 3-mm diameter electrodes were made of the Cr-Mo-V alloy steel used as the substrates. A silver chloride electrode was used as a reference electrode, with results converted to a hydrogen electrode reference.
Results and discussion
As the experiments showed, during tensile testing, some variation in behavior was noted. In the case where the cyanoacrylate adhesive is applied to an unplated test sample (4), the tensile force at fracture is considered to be the strength of the adhesive joint. For a plated test sample (4), when separation occurred at the plated metal/basis metal interface, the tensile force at fracture can be taken as the bond strength between the plated coating and the basis metal.
Our test results are shown in Table 2. The strength of the adhesive joint proper was found to be 400-410 N. In all of our plated samples, separation occurred at the plated metal/basis metal interface, indicating that the strength of the adhesive joint exceeded the strength of the bond between the plated coating and the basis metal. The results also show that the bond strength values for the zinc deposits were appreciably higher than those for copper.
Table 2 - The effect of plating metal and the electrolyte composition on the bond strength.
Plated coating | Tensile force at fracture (N) |
No plating | 400-410 |
Sulfate copper | 50-55 |
Pyrophosphate copper | 80-85 |
Sulfate zinc | 106-112 |
Pyrophosphate zinc | 180-191 |
Moreover, the bond strength for one kind of plating depends on the composition of electrolyte. Thus, the bond strength of the copper electrodeposited from the pyrophosphate electrolyte is 30 N higher than that of copper plating electrodeposited from the sulfate electrolyte. The difference in the bond strength for the zinc electrodeposited from the corresponding electrolytes is even more significant, 74-79 N.
It is known that, with all other things being equal, the bond strength between an electroplated coating and its basis metal depends on the cathodic polarization - the higher it is, the higher is the bond strength.3 The results obtained by us are completely in agreement with this premise. Thus, at the cathodic current density of 1.0 А/dm2, the cathode polarization in the copper pyrophosphate electrolyte is 0.8 V higher than that in the sulfate electrolyte (Fig. 2). For zinc plating, the difference in the cathode polarization is also rather appreciable, 0.5 V. As plating electrolytes for the same metal with differing compositions cause differing cathode polarization behaviors (Fig. 2), so too do the bond strengths vary (Table 2).
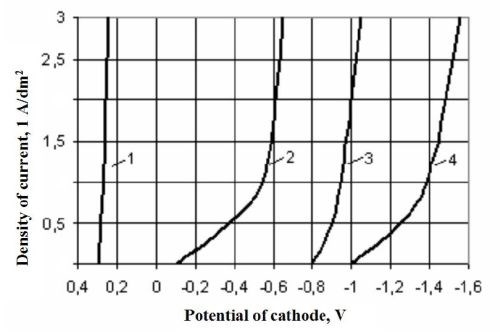
Figure 2 - Cathodic polarization curves. The number of each curve corresponds to the number of the electrolyte listed in Table 1.
Conclusions
A simple and reliable for the quantitative determination of the bond strength of electroplated coatings on steel by means of an adhesive joint tensile test is suggested. This method can be used for research purposes, and in particular, in designing new electrolytes for electrodeposited coatings, and under working conditions for monitoring the quality of such coatings.
References
1. Russian Standard GOST 9.302-88. Unified system of corrosion and ageing protection. Metal and non-metal inorganic coatings. Control methods.
2. M.A. Shluger (Ed.) Electroplating in Mechanical Engineering, in two volumes, Mashinostrojenie, Moscow, Russia, 1985.
3. V.V. Artamonov & V.P. Artamonov, Optimization of the Control and Technical Diagnostics of Heat Power Equipment, Nauka, St.-Petersburg, Russia, 2009.
E-mail: vaart1@mail.ru