Mineral acids like hydrochloric and sulfuric have been used in metal finishing from the beginning. Acid salts have also been available for many years. The benefits of using acid salt in place of mineral acids have been overlooked in many applications.
This article discusses a few of the reasons for replacing mineral acid with acid salt, which include:
Featured Content
-
Improved activation of alloyed brass resulting in reduced scrap.
-
Improved activation of alloyed steel resulting in reduced scrap.
-
Corrosive action of hydrochloric fumes on equipment and finished parts.
-
Environmental considerations on water treatment of spent acids and rinse water.
-
Operator safety when handling mineral acid versus acid salt.
-
Total operating cost when considering scrap, fumes, water treatment, and safety.
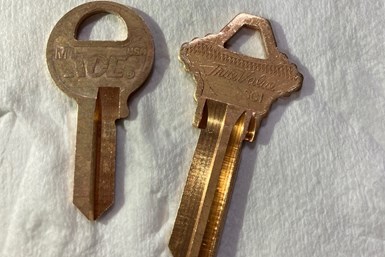
The key on the left was pickled with sulfuric acid, resulting in a somewhat darker and less uniform appearance. The key on the right was pickled with Acid Salt.
Photo Credit: Hubbard-Hall
Activation of brass alloys — sulfuric acid vs. acid salt
Sulfuric acid (H2SO4) is often used for pickling brass. Much like hydrochloric acid (HCL), it is extremely aggressive on the parts base metal. Brass parts — especially machined or stamped parts — generally also contain alloying agents to improve the machinability and stamping properties of the material.
For example, 360 brass contains a 60/40 mixture of copper and zinc with about 3% lead. Sulfuric acid will tend to dissolve the zinc in the alloy preferentially to copper and lead. Lead is the least soluble. Over pickling can lead to removing most of the zinc from the surface of the part, leaving a copper/lead-rich alloy. This can lead to a reddish mottled appearance of the parts. The lead-rich surface makes it difficult and less reliable for good adhesion when nickel plating.
Acid salt-containing fluoride will minimize the attack on the base metal and solubilizes the lead presenting a clean, active surface for plating. Acid salt may also contain surfactants that aid in keeping the parts active and water break free after pickling.
Activation of alloy steel using hydrochloric acid vs. acid salt
Hydrochloric acid is very aggressive at dissolving iron but does not dissolve the alloying agents in steel at the same rate. This can lead to difficulties, especially with machined parts, which are usually made from alloy steel such as 12L14.
This material contains lead as a lubricant to improve its machinability. The function of the lead in the alloy is to flow over the surface of the part as it is machined to provide lubrication at the tool/part interface. This leaves a coating of lead on the surface of the parts after machining. Over pickling in HCL preferentially dissolves iron leaving the alloying agents like lead, carbon, manganese, and other alloying agents on the surface of the part. This can lead to poor adhesion in nickel plating, grainy deposits in phosphate coatings, and irregular smears in black oxide.
Acid salt containing a small amount of fluoride salt will often eliminate these issues. Acid salt is pH buffered, minimizing the chances for over attack on the part, while the fluoride component will dissolve a small amount of lead or other alloying metal films. The result is a clean, active surface ready to accept whatever coating is applied.
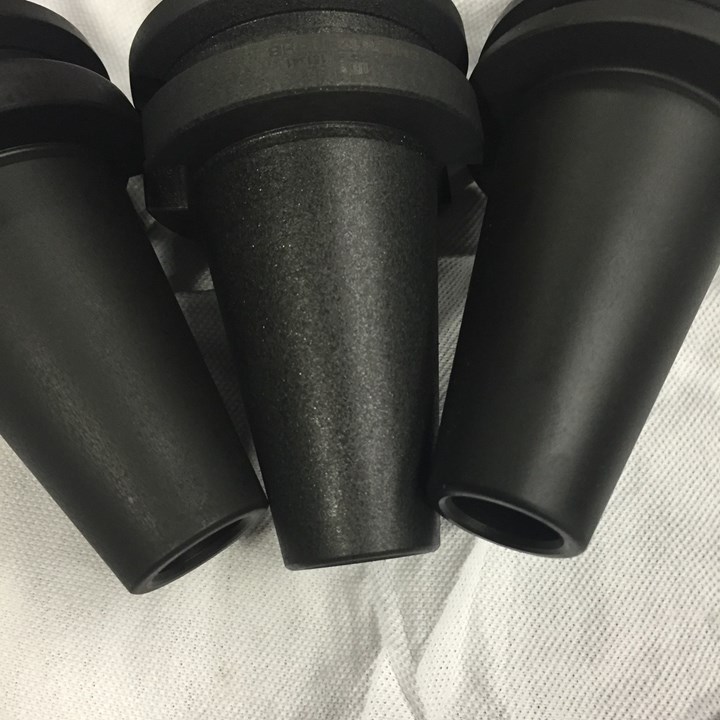
Manganese Phosphate over Machined Steel Parts. The middle part was Pickled with HCL; parts on the outsides were pickled with Acid Salt. Note the grainy appearance of the middle part. Photo Credit: Hubbard-Hall
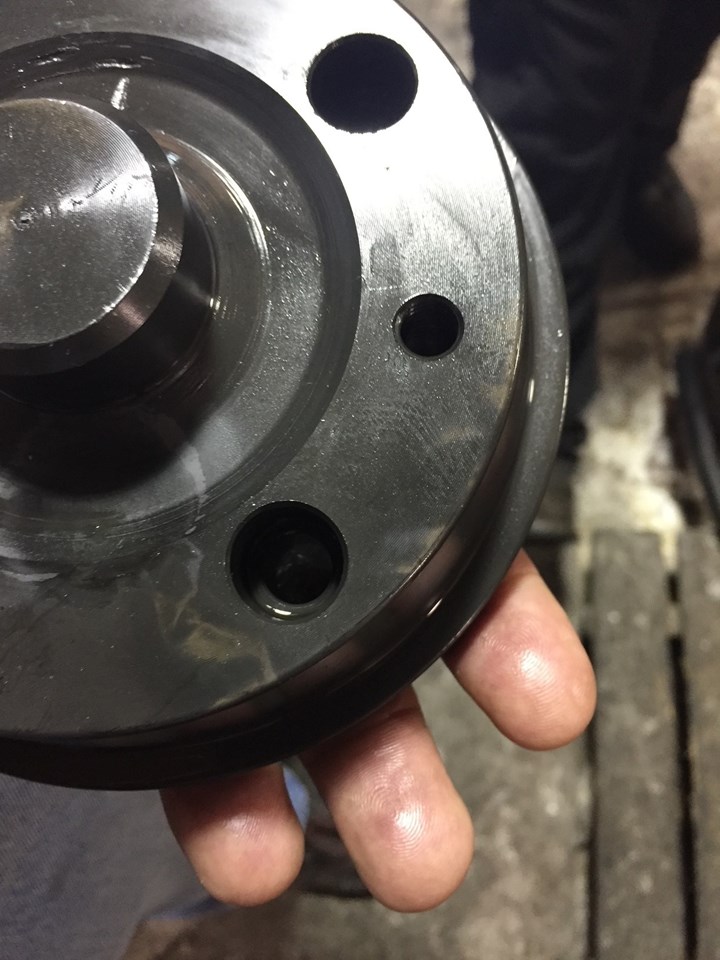
Black Oxide over Machined Steel showing smear streaks. Photo Credit: Hubbard-Hall
Corrosive action of hydrochloric acid
HCL is commonly used for pickling steel, but here are some drawbacks to using it. HCL is chlorine gas dissolved into water. Over time the chlorine gas will evaporate and lower the HCL concentration. This is like soda going flat when left unbottled for too long. This requires additions of HCL and sometimes requires decanting the bath to make room. The HCL tank is constantly releasing fumes into the plant, which is corrosive to equipment and finished parts.
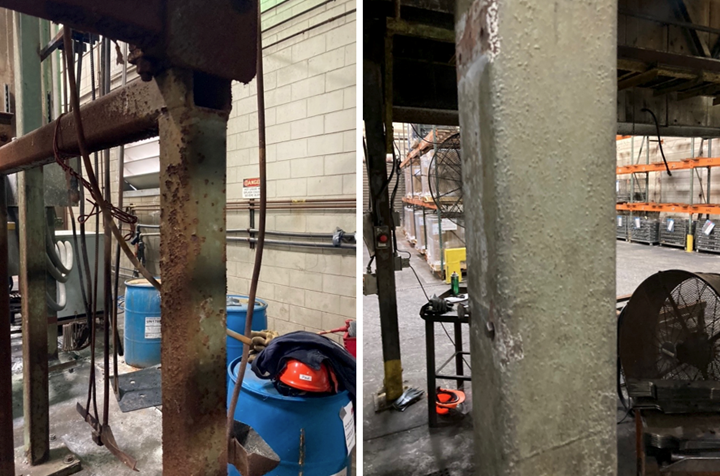
The beam on the left is near an HCL tank. The beam on the right is the same age, runs the same process, but does not include an HCL tank. HCL is very corrosive to equipment.
Photo Credit: Hubbard-HallEnvironmental concerns
Water treatment is always an important consideration in metal finishing. Acid salts have high ionic strength but a buffered pH. This allows for effecting pickling with less attack on the base metal. Less attacks result in less metal in the acid bath and less metal dragging into the rinse water. The result is fewer metals needed to be treated and less sludge formed.
-
Lower concentration of metals in the effluent stream using acid salt as an activator.
-
Less caustic is needed to adjust pH in water treatment using acid salt compared to sulfuric.
Often acid salt baths will last longer, requiring fewer dumps due to the slow build of metals.
Safety and handling: liquid vs. powder
Liquid acids are used in many finishing and waste treatment applications. The inherent safety-related issues are well known. Trained personnel, using proper technique and precautions, handle and use these acids without harmful effect. Nevertheless, accidents have been known to happen.
Where possible, moving from a hazardous material to one that is less hazardous will reduce the chances of a mistake. Here is a look at liquid minerals and powdered acid salts, as well as a health and shipping data comparison.
Liquid Mineral Acids — These usually refer to hydrochloric and sulfuric acid. Safety-related issues include:
-
Mineral acids can cause rapid and severe burning of exposed skin. Hydrochloric acid generates dangerous fumes.
-
Additions to tanks must be made gradually with good mixing. Sulfuric acid is especially exothermic, rapidly giving off heat, resulting in localized boiling and splash-back.
-
Extreme care is necessary to prevent potentially catastrophic accidents. Accidental mixing of hydrochloric acid with sulfuric or nitric acid can generate chlorine gas. Think mustard gas from WWI.
-
Empty carboys, drums, and totes of acids should be returned for refill promptly. Reducing hazard clutter is important to handling safety.
-
Shipping liquid sulfuric or hydrochloric acid in plastic drums creates the possibility of the drums being forked or pierced and leaking during transit. This could be dangerous for the shipping contractor as well.
Powdered Acid Salt — Acid salts have been available to finishers for many years. These products were specifically developed to increase the effect of acid treatments in a safer handling situation.
-
Acid salts ionize to provide active acid in the bath. Sodium bisulfate is the acid salt of sulfuric acid. The safety benefit is eliminating the handling of sulfuric acid and the exothermic heating when blending it.
-
Acid salts are blended to offer additional acid accelerators in the form of chlorides and fluorides. These agents also ionize in solution, providing hydrochloric and hydrofluoric acids. One concentrate product can eliminate the handling of two or three separate generic acids.
-
Powdered acids may contain surfactants and wetting agents. These allow for improved penetration for surface action.
-
Surfactants in powdered acids can form a stable light foam blanket. This may effectively eliminate over 99% of potentially corrosive fumes and mists.
-
Powdered acids are buffered, thereby extending the bath service life. The benefits include less frequent solution dumps and, therefore, less handling requirements.
Health and Shipping Data Comparison: Activation is the next crucial step after cleaning in the surface preparation sequence. Where safety and handling are concerned, powders offer an advantage.
MFPA Rating, Comparison
Health |
Flammability |
Reactivity |
Shipping |
||
Acid Salt W: |
1 | 0 | 0 |
Not DOT Reg. |
Not DOT Reg. |
Sulfuric: |
3 | 0 | 2 |
UN 1830 |
8 Corrosive |
Hydrochloric: |
3 | 0 | 1 |
UN 1789 |
8 Corrosive |
Total Operating Cost
At first, acid salts may appear more expensive than “cheap” mineral acids. Considering the total operating costs, this is often a false economy. A slight increase in makeup cost is offset by many factors, not the least of which is rejection from the production line.
This alone justifies the use of acid salt, especially when machined stamped parts are being processed. Factors include:
-
More reliable production performance on machined and stamped parts.
-
Fewer pickling bath make-ups and additions.
-
Less corrosion of equipment and parts in storage.
-
Fewer metals in the effluent rinse water.
-
Safer for operators.
Boiling from mixing, buffered pH, fumes, spills.
Catastrophic accidents from accidentally mixing with incompatible chemicals.
Summary and Conclusions
Acid salt is good for the bottom line, equipment, operator safety, and water treatment in many applications. This results in an operating cost reduction while improving health and safety concerns. Newer developments include “liquid” versions of acid salt if the convenience of pumping the solution is desired, while many of the benefits of salt are maintained.
RELATED CONTENT
-
Cleaning Limescale from Galvanized Steel
How do you clean white lime scale and rust spots on galvanize?
-
The Hull Cell: Key to Better Electroplating - Part II
How to use it for planning, preventive maintenance and troubleshooting.
-
Cleaning Prior to PVD/CVD Coating
Determining the cleanliness and chemical de-coating of PVD/CVD layers.