Selecting the Right Outdoor-Durable Powder Coating
The powder coating industry offers an array of chemistries to provide an excellent match to the manufacturer’s expectations for outdoor durability.
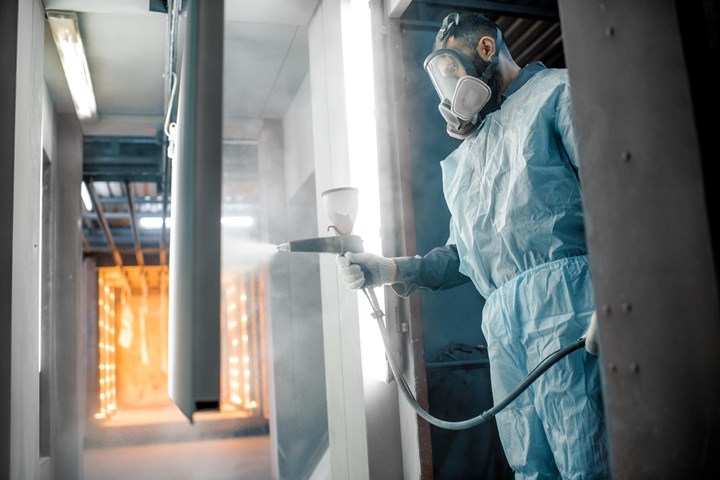
Selecting an outdoor durable-grade powder coating to meet the needs of a customer requires the careful analysis of options, costs, and specifications. Source | Getty Images
Choosing an exterior-durable powder coating can be a daunting task. Some powder pundits assign the descriptor “outdoor durable” on a product without a thorough understanding of what this really means. In practice, it is important to consider the differing levels of exterior durability and which powder chemistries meet which quality specifications.
Powder coatings are based on a binder comprised of a resin and curing agent, colorant pigments, extenders (fillers) and additives. The combination of UV light and moisture attacks the chemical bonds in polymers and pigments, resulting in color fade, chalking and the degradation of barrier properties intended to protect a substrate. Polymers and pigments possess intrinsic resistance to this degradation based on their molecular composition.
Featured Content
What does outdoor durability mean?
Describing a powder coating merely as “outdoor durable” is inexact and does not provide sufficient information to select a product to meet a customer’s requirements. Coatings are delineated based on weathering metrics from actual locations that receive high levels of UV exposure. In North America, coastal south Florida is most used as the standard location to evaluate exterior durability.
Standard-grade outdoor-durable powder coatings are sometimes described as industrial or entry-level architectural grade. These coatings maintain color and gloss for 12 to 18 months of south Florida exposure. After two years, these coatings exhibit significant color fade and 50% or more gloss reduction. Rich and dark colors show the most visual change, as degradation is typically represented as a white, chalky phenomenon.
Entry-level architectural-grade powders fit this performance profile and are used for items that experience only incidental UV exposure or are not expected to maintain appearance past a few outdoor seasons. Storm doors, consumer garden equipment, bicycles and lower end lawn furniture are examples of products coated with standard-grade outdoor-durable powder coatings.
High-performance exterior durability describes a class of coatings expected to withstand up to five years of exposure in south Florida before exhibiting visible evidence of degradation. These types of coatings are used for general-purpose architectural applications such as consumer window frames, architectural hardware, and high-quality outdoor furniture. Some automotive trim products, wheels and agricultural implements use this technology as well.
In addition to providing high gloss and smoothness, exterior automotive-grade coatings require outstanding resistance to sunlight, moisture, air pollution (mainly acidic) and thermal shock. These coatings must maintain gloss and color for a service life up to and beyond 10 years.
Exterior automotive body coatings are typically comprised of a multi-layer system including electrodeposition primer, primer-surfacer, basecoat and clear topcoat. Luxury-model alloy wheels typically use a basecoat/clearcoat system and require similar durability. Acrylic-based powder coatings are used for these applications as they possess the UV durability, chemical resistance and excellent appearance required by these demanding specifications.
Superior-performing (sometimes referred to as “hyperdurable”) architectural-grade powder coatings require 10 years’ durability without exhibiting significant film degradation. These coatings are specified for monumental end uses such as commercial buildings, skyscrapers and the like.
Chemistries
A survey of powder coating chemistries provides a matrix of options for outdoor-durable requirements. To start with, epoxy-based and hybrid (epoxy polyester) powders are not outdoor durable. Any epoxy content in a powder coating will cause the finish to chalk and degrade in less than a couple months of exposure to sunlight.
Entry-level or industrial-grade exterior-durable powder coatings include polyester-TGIC, polyester-HAA, and polyurethane chemistries. These economical coatings are available in a limitless variety of colors, gloss, and special effects.
High-performance architectural and general-purpose powders are usually based on “superdurable” resin technology and are available in polyester-TGIC, polyester-HAA and polyurethane platforms. Color possibilities are extensive but not as limitless as those available in an industrial-grade product because high-performance pigment options are more limited. Standard-grade organic pigments fade in 18 to 24 months of outdoor exposure. High-performance powder coatings must use either inorganic mixed-metal oxide pigments or high-performance automotive-grade organic pigments to meet color and durability requirements.
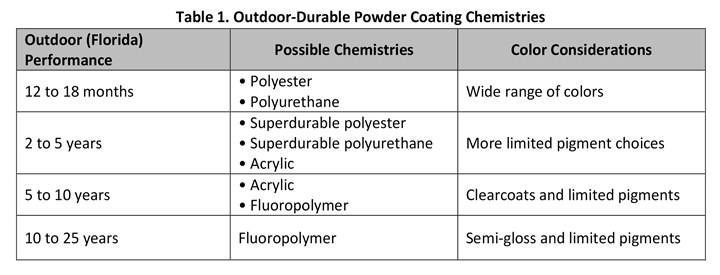
While polyester and polyurethane powder coating chemistries last 12 to 18 months, fluoropolymer can last up to 25 years. Source: ChemQuest Powder Coating Research
Exterior automotive-grade powder coatings are most often high-gloss clearcoats, silver metallics and black trim coatings. Color is limited, as formulators must use expensive high-performance pigments. This product space is dominated by acrylic resin technology and has an impressive track record of performance on BMW cars.
Specialty polymers based on thermoset fluoropolymer chemistry are required to meet superior-performing architectural-grade powder coating specifications. These coatings resist fading and film degradation for a minimum of 10 years in the south Florida climate; however, studies have shown this chemistry to withstand 20 to 30 years in the field. Color is limited to muted hues generated by inorganic mixed-metal oxides and gloss levels typically below 70 GU (gloss unit).
Specifications
Each industry and often each manufacturer have their own specifications that define the performance requirements for coatings used on their products. The architectural industry has a very good set of standards established by the American Architectural Manufacturers Association (AAMA) in the U.S. and Qualicoat and GSB in Western Europe and Australia (see Table 2).
All car manufacturers have the expectation that the coating must last at least 10 years without evidence of significant fade, discoloration, cracking, or erosion of the finish. Most automotive companies use a combination of accelerated exposure test methods and natural outdoor testing. Source: ChemQuest Powder Coating Research
Automotive body topcoat specifications are established by each car manufacturer, but all have the expectation that the coating must last at least 10 years without evidence of significant fade, discoloration, cracking, or erosion of the finish. Most automotive companies use a combination of accelerated exposure test methods and natural outdoor testing.
The most common exterior automotive use of powder coatings is as a clearcoat for alloy wheels. General Motors’ 9985586 specification requires three years’ Florida durability of cosmetic qualities. For trim parts, their 9984047 specification calls for an acrylic powder topcoat requiring five years’ durability.
Test methods
Scientists have worked for decades to simulate outdoor conditions in the laboratory in an attempt to accelerate the degradation process. The goal is to establish a rapid predictor of weathering performance to correlate to long-term exposure.
Historically, the Q-Lab QUV Accelerated Weather Tester has been the predominate technique to assess outdoor durability. ASTM D4587 describes QUV testing, which entails alternating cycles of humidity and UV energy generated from fluorescent lamps. These lamps are categorized as UVA 340, UVA 351, FS-40, and UVB-313EL. Details are listed in Table 3.
ASTM D4587 describes QUV testing, which entails alternating cycles of humidity and UV energy generated from fluorescent lamps. These lamps are categorized as UVA 340, UVA 351, FS-40, and UVB-313EL. Source: ChemQuest Powder Coating Research
It is crucial to understand the effect various lamps have on powder coating chemistries and how valid the results may be. UVA lamps more closely approximate sunlight than UVB lamps and take longer to degrade powder coating polymers. UVB lamps emit unnatural short-wavelength energy (below 295 nm) that more aggressively damages powder resins, especially polyester types. Hence, the use of accelerated UVB test conditions generates evidence of coating failure significantly faster than UVA testing. Standard-grade polyesters fail within 250 to 300 hours of UVB exposure, whereas the same products last over 1,000 hours in UVA testing.
A more accurate test protocol uses the Xenon arc weatherometer (ASTM D7869). Xenon arc testing closely approximates the wavelength of sunlight and combines it with a humidity cycle. Exposure is measured in MJ/m2 (megaJoules per square meter) of energy and can be correlated to actual outdoor exposure. Some weathering experts use 275 MJ/m2 as a measure of a typical year of south Florida exposure. Xenon arc test cabinets emit about 0.55 W/m2 light energy per hour, which equates one year of south Florida exposure to about 2,360 hours in the cabinet using a cycle of 2 hours light to 1 hour dark with humidity.
In addition to real-time natural exposure in south Florida, the most realistic measure of UV durability uses a solar concentrating technique described in ASTM D4141 and D4364. This technique provides an acceleration of natural UV degradation by reflecting sunlight onto a coated surface with an arrangement of 10 mirrors. Test racks are stationed in central Arizona and include a water spray feature to accelerate degradation.
Using this method, approximately 1,400 MJ/m2 of solar energy is delivered to the coating surface in one year. This correlates to 10 to 12 years of natural south Florida exposure. Solar concentration test methodology is highly accurate but very expensive to conduct.
Making the ideal choice
Selecting an outdoor durable-grade powder coating to meet the needs of a customer requires the careful analysis of options, costs, and specifications. The powder coating industry offers an array of chemistries to provide an excellent match to the expectations of the manufacturer. Understanding which products meet industry standards for weatherability is a good foundation for making the right selection for your customer.
About the Author
Kevin Biller
Kevin Biller is the director at ChemQuest Powder Coating Research. For more information, contact kbiller@chemquest.com or visit chemquest.com/cqpcr.
RELATED CONTENT
-
Powder Coating Week 2024 Offers Education and Networking
On March 11-13, 2024, this event for powder coaters will combine training, presentations, technical sessions, tabletop exhibits, roundtable discussions, expert panels and social activities.
-
Powder Coating Aluminium Adhesion Failure
PF columnist Rodger Talbert offers advice for mitigating adhesion failure of powder coating on aluminum parts.
-
Proper Sieve Size for Powder Coating's Smooth Results
Kevin Biller at ChemQuest Powder Coating Research gives recommendations for sieve size to ensure surface smoothness.