Developing Standardized Testing for Trivalent Chromium Thickness: A Progress Report
The industry shift toward trivalent decorative chromium plating and away from hexavalent highlights a need for testing standards. As Chair for ASTM B08.10 Subcommittee on Test Methods for Metallic and Inorganic Coating, Mark Schario is leading the committee’s focus on developing standardized testing for trivalent chrome thickness. This presentation provides information on the initiative, testing methods and variables, initial data on thickness comparison and alloy composition, and summary of input and extended lab testing.
#regulation #nasf #surfin
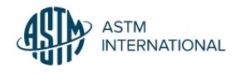
B08 Test Methods
Workgroup AC574 -WK74450_B568-98(2014)
A Paper* based on a Presentation given at NASF SUR/FIN 2021 (Detroit, Michigan)
by
Mark Schario**
Columbia Chemical Corporation
Brunswick, Ohio, USA
Editor’s Note: The following is a paper based on a presentation given at NASF SUR/FIN 2021, in Detroit, Michigan on November 2, 2021, in Session 2, New Trends and Advances in Surface Finishing / Engineering. A pdf of this brief can be accessed and printed HERE; the complete Powerpoint presentation is available by clicking HERE.
Featured Content
ABSTRACT
The industry shift toward trivalent decorative chromium plating and away from hexavalent highlights a need for testing standards. As Chair for ASTM B08.10 Subcommittee on Test Methods for Metallic and Inorganic Coating, Mark Schario is leading the committee’s focus on developing standardized testing for trivalent chrome thickness. This presentation provides information on the initiative, testing methods and variables, initial data on thickness comparison and alloy composition, and summary of input and extended lab testing.
Overview
The industry shift toward trivalent decorative chromium plating and away from hexavalent highlights a need for testing standards. As a result, the ASTM B08.10 Subcommittee on Test Methods for Metallic and Inorganic Coating (within the ASTM International Metallic and Inorganic Coatings Committee (B08)), along with the United States Council for Automotive Research (USCAR) have focus on efforts to identify the best practices for thickness determination of trivalent chromium deposits in decorative applications. These deposits are not pure chromium. Indeed, their composition is more that of an alloy, and this factor must also be taken into account. Based on testing, the intent is to modify existing ASTM Standards or create new standard(s) to meet the needs of decorative electroplating on multiple substrates. Further, additional information such as variables in electrolyte composition and current density will be useful for engineering and OEMs in their individual or manufacturer specifications.
This work affects the following test methods:
- ASTM B-568 Standard Test Method for Measurement of Coating Thickness by X-Ray Spectrometry
- ASTM B-504 Standard Test Method for Measurement of Thickness of Metallic Coatings by the Coulometric Method
- ASTM B-556 Standard Guide for Measurement of Thin Chromium Coatings by Spot Test
The following plating standards are also affected:
- ASTM B-456 Standard Specification for Electrodeposited Coatings of Copper Plus Nickel Plus Chromium and Nickel Plus Chromium
- ASTM B-604 Standard Specification for Decorative Electroplated Coatings of Copper Plus Nickel Plus Chromium on Plastics
The decorative plating layers for hexavalent and trivalent chromium systems are compared in Fig. 1. In the hexavalent system (Fig. 1a), The chromium provides a hard passive layer and white color. The microporous nickel provides porosity and prevents undercutting of the chromium layer. The sulfur-containing bright nickel acts as the sacrificial layer, while the high sulfur nickel is anodic to the bright and semi-bright layers. The semi-bright nickel layer prevents corrosion to substrate. The trivalent chromium system differs in the upper layers (Fig. 1b). Here, the chromium provides hard a passive layer and white color, plus microporosity. The underlying low sulfur strike prevents undercutting of the chromium layer. The three lower nickel layers act the same in both systems.
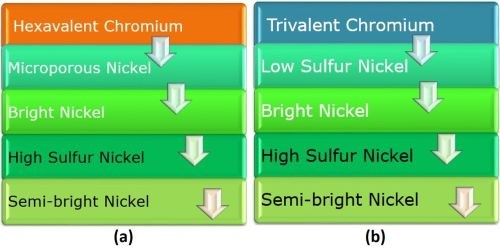
Figure 1 - Comparison of (a) hexavalent and (b) trivalent chromium overlays on four-layer nickel.
Review of test methods and variables
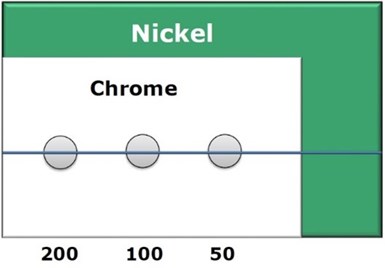
Figure 2 - Test panel layout.
All test specimens were prepared by plating a steel Hull Cell panel with a uniform bright nickel layer, rinsing, then applying the chromium layer to provide different current densities (Fig. 2), 50, 100 and 200 ASF. Three chloride-based trivalent chromium solutions were studied:
- White trivalent chromium
- Black trivalent chromium (low concentration blackening agent - 7.5 mL/L)
- Black trivalent chromium (medium concentration blackening agent - 17 mL/L)
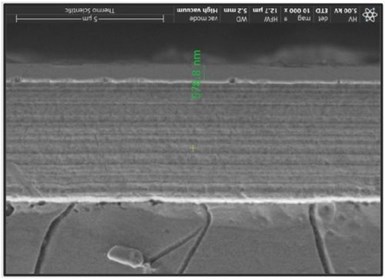
Figure 3 - Typical SEM cross-section image (Cr thickness shown as 574.8 nm).
All samples were plated in same Hull Cell with air agitation. The Hull Cells were first tested by x-ray spectrometry, according to ASTM-B-568, a non-destructive test, then tested in same spot with the coulometric test (ASTM B-504). This is a destructive test and is the most common test method used in the industry.
The Hull Cell panels were then cut down the center of the dissolved area so SEM measurements could be made directly adjacent to the area already tested. Samples were then polished and examined using the SEM cross-section for the final thickness measurement (ASTM B-748)(Fig. 3). This direct measurement served as the benchmark for comparing the other methods.
Two separate samples were retained in the same area for a surface measurement of composition, and finally sent out for the Calotest, a destructive test. In the test, a ball-cratering method is used, wears through the chromium layer, then measures the thickness by the width in relation to the diameter of the wear ball. One can quickly characterize coating thicknesses between 0.1 μm and 50 μm on a wide range of materials.** The Calotest results are still pending as of the writing of this report.
Initial round of testing
Thickness Comparison
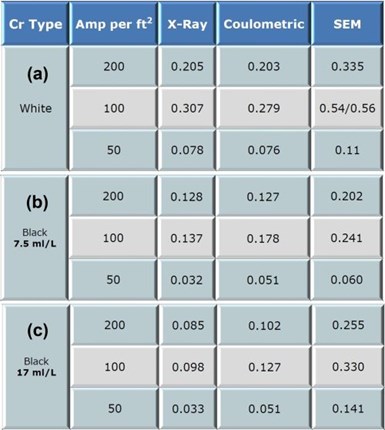
Figure 4 – Summary of thickness testing: (a) white Cr(III); (b) low concentration black Cr (III); (c) medium concentration black Cr(III).
The thickness testing results are summarized in Fig. 4. It can be seen that there is considerable variation in results between the benchmark SEM measurements and the x-ray and coulometric results. The initial SEM measurements yielded higher thickness values than either the x-ray or coulometric testing.
The black trivalent electrodeposits yield an even greater disparity than white trivalent chromium electrodeposits. The variance between the x-ray and coulometric results tended to increase as the concentration of blackening agent was increased. This is particularly evident in Fig. 5, where the ratios between the x-ray and SEM benchmark values are displayed.
It is clear that suppliers should provide factor when using x-ray or coulometric testing to provide applicators guidance on actual plating thickness.
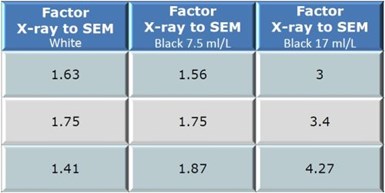
Figure 5 - Comparison of x-ray to SEM factors with increasing blackening agent concentration.
Alloy composition
The alloy composition was determined by energy-dispersive X-ray spectroscopy (EDX). Selected results are compared for the three Cr (III) solutions for a current density of 100 ASF and are shown in Fig. 6.
We found that measurement of the alloy composition was affected by penetration of the x-ray beam through the chromium layer into the nickel layer. The decorative chromium thickness was too thin for this method. Thicker coatings will be needed to get accurate elemental composition information. Further testing using EDX will require thicknesses greater than 0.5 microns.
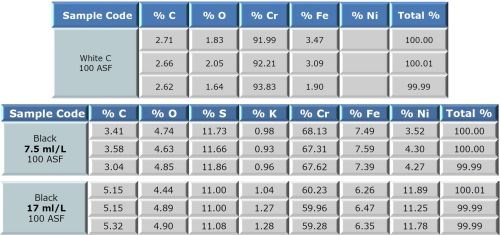
Figure 6 - Alloy composition of specimens from the three Cr (III) solutions at a current density of 100 ASF.
Future work
The Calotest is being checked by Anton Parr as an optional destructive test method. Additional companies are being researched for this test. Based on the differences identified, a round robin test phase is being organized, recruiting labs which can provide necessary thickness testing on known samples. Then, the plating of large panels for distribution is planned once the round robin testing labs are identified.
About the author
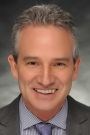
Mark Schario is Executive Vice-President at Columbia Chemical Corporation, headquartered in Brunswick, Ohio. He joined Columbia Chemical in 2010 as Vice President, Technologies and now serves as Vice President, Global Business Development for the company. He has over 30 years of experience in the surface finishing industry. Mark also functions as the company’s top liaison to the automotive industry and is Committee Chair to ASTM B08 on Metallic and Inorganic Coatings which has jurisdiction over 132 standards. He is a member of the NASF and has earned the industry designation of CEF/Certified Electroplater-Finisher. Mark holds an Executive MBA from the Weatherhead School of Management at Case Western Reserve University.
*Compiled by Dr. James H. Lindsay, Technical Editor - NASF
** Corresponding author:
Mark Schario |
**Anton Paar USA, Inc, Calotest Series, Ashland, Virginia.
RELATED CONTENT
-
A Process for Alkaline Non-cyanide Silver Plating for Direct Plating on Copper, Copper Alloys and Nickel Without a Silver Strike Bath
Traditionally, silver is electroplated in toxic, cyanide-based chemistry. Due to cyanide’s extreme hazard to human health and environments, developing non-cyanide silver chemistry is essential for the silver electroplating industry. Discussed here is an aqueous, alkaline non-cyanide silver plating technology, which can be directly plated over nickel as well as copper and its alloys. The silver deposits have perfect white color and better anti-tarnishing properties than other non-cyanide silver processes. The silver is plated entirely from the dissolving silver anode and the bath is very stable, and maintains a stable pH level both during plating and idle time. This new non-cyanide silver technology will plate bright silver that is perfectly suitable for electronic, industrial and decorative applications. .
-
Development of a Sustainability Metrics System and a Technical Solution Method for Sustainable Metal Finishing: AESF Research Project #R-121, 6th Quarterly Report
The NASF Research Board has funded a research grant at Wayne State University on sustainability in the surface finishing industry, under the direction of Professor Yinlun Huang. The objective of the work is to create a surface-finishing-specific sustainability metrics system to measure economic, environmental and social sustainability. In this report, a benchmarking study of five plants was undertaken to illustrate how the sustainability assessment works.
-
PFAS and the Surface Finishing Industry
NASF and its member companies have a long history of environmental stewardship, especially when it comes to PFAS.