Episode 25: An Interview with Darren Howard, Circle-Prosco Inc.
As phosphate-based pretreatments become increasingly regulated, more finishers are considering zirconium pretreatment solutions. Darren Howard, a key account manager with Circle-Prosco, Inc., discusses the increasing popularity of zirconium pretreatment use in such areas as automotive and agriculture.
Edited by Scott Francis
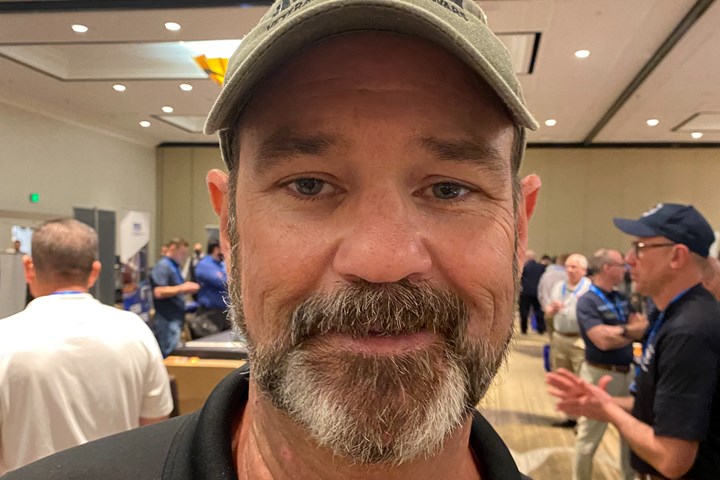
Darren Howard, key account manager, Circle-Prosco Inc.
Photo Credit: Products Finishing
Stream the interview with Darren Howard here or read an excerpt of the interview below.
Zirconium pretreatments have come a long way. As phosphate-based pretreatments come under increasingly strict regulations, advances in zirconium pretreatment technology see them attracting more interest. Recently, Products Finishing sat down with Darren Howard, a key account manager with Circle-Prosco, Inc., a company that started in the automotive heat exchange space but has been working to take its specialized pretreatment processes into such areas as industrial and agriculture. Howard has worked with numerous OEMs in both the automotive and agricultural sectors. In this interview, he discusses his experience and what he loves about working with zirconium pretreatments.
Featured Content
Tell me about your background and how you got your start with Circle-Prosco.
I started in the automotive industry in 1998 working with General Motors. Before starting as an engineer, I learned to be a production supervisor. That was one of the biggest learning advantages for me — you get to learn it from the people side before you even dig into the process side. And then, once I got into the coatings and the engineering training, it was very immersive. It was a great program that grounded me for my career moving forward.
I've now worked in automotive, agriculture and heavy equipment. Also, not too long ago, I worked for a bolted tank company that makes bolted tanks for wastewater treatment or potable water — an application that has to hold up to some abrasive environments.
I've designed and constructed paint lines, and I've also managed the processing end of paint lines.
You’ve had a lot of experience working with various preatments with a variety of markets. What is unique about Circle-Prosco’s pretreatment?
The thing that jumps out to the front is that you no longer have to worry about phosphates. You don't have the heavy metals in either the cleaner or the zirconium itself. You can't turn on the news today without hearing about green initiatives, and several states have said that phosphates are going to be eliminated. I worry that manufacturers aren't hearing that unless they happen to live in one of those three states. It's something that I'm trying to get into people's thinking space, “hey, this is coming, whether you want to do it or not.”
Second is the simple fact that with zirconium, you do not have to now deal with sludge (which is a byproduct of your iron phos and your zinc phos). When you think about what you’re eliminating by getting rid of that sludge, you can quickly see the benefit. Dealing with sludge means following regulations set by your local Department of Natural Resources (DNR) and your state Environmental Protection Agency (EPA) — you've got to really manage that process tight. On top of that, it costs money — it takes time to deal with and it’s part of somebody’s job description. In addition, with an iron or zinc phos, you have to perform a boil out or descale operation every so often to keep sludge from building up in your tank and, if you perform spray, getting gunk into your spray nozzles. And, if you don't get a good spray, then you're not getting a good cleaning or ultimately getting a good coating.
What trends are you following in the manufacturing world? We talked a bit about agriculture, but what other markets or applications are a good fit for this technology?
The electric vehicle market is really driving a lot of attention [for zirconium].
Zirconium has great conductive properties and can improve throw power for ecoat, for example — meaning you can build to your desired thickness more quickly. That conductivity is part of why the FCC and DOD use it for electronics and defense applications.
As you look at EV applications such as battery plates, the amount of movement in that industry is huge and it’s not only going to be automotive — it’s also in tractors and the agricultural sector.
What do you like most about CP’s zirconium pretreatment?
Zinc phos has always been kind of thought of as the king for performance. Steelcote is right there with it. And, in some cases, depending on specific processes, we're actually beating it. I think if people could get away from the stigma that a nanoceramic can’t offer as good a performance product as metal, they would be shocked at what they're going to see.
RELATED CONTENT
-
Cleaning Prior to PVD/CVD Coating
Determining the cleanliness and chemical de-coating of PVD/CVD layers.
-
Are TGIC-Free Powder Coatings Right For You?
This alternative to TGIC-based polyester powder coatings offers similar performance and enhanced transfer efficiencies.
-
The Hull Cell: Key to Better Electroplating - Part II
How to use it for planning, preventive maintenance and troubleshooting.